I. Introduction
The CNC press brake is a sophisticated sheet metal processing machine that requires precise operation under the hydraulic control of both a CNC controller and an operator in sheet metal fabrication and manufacturing industries. It is important to carefully set the necessary parameters and procedures before beginning a bending job.
However, even with proper preparation and maintenance, the press brake bending machines can still experience mechanical failures over time. Common issues include vibrations during bending, oil pump leaks, and inaccurate size and shape of the finished workpieces, leading to material waste and even damage to the machine.
In some cases, these faults can also pose a risk to the safety of the operator. In this blog, we will explore the reasons for errors in press brake bending and offer tips on how to prevent and avoid them.
II. Troubleshooting Common Issues with Press Brake Machines
1. The machine is not kept clean
Neglecting to keep the press brake clean is a common issue in its usage. Over time, accumulated dirt can cause parts and molds to wear down. Debris can even scratch the workpiece and the presence of dust can impact the machine's operation.
To prevent these issues, it is important to clean the hydraulic bending machine and its tools both before and after use. All debris, oil, and dust should be removed to prevent dust from infiltrating the machine. Regular cleaning can extend the machine's lifespan.
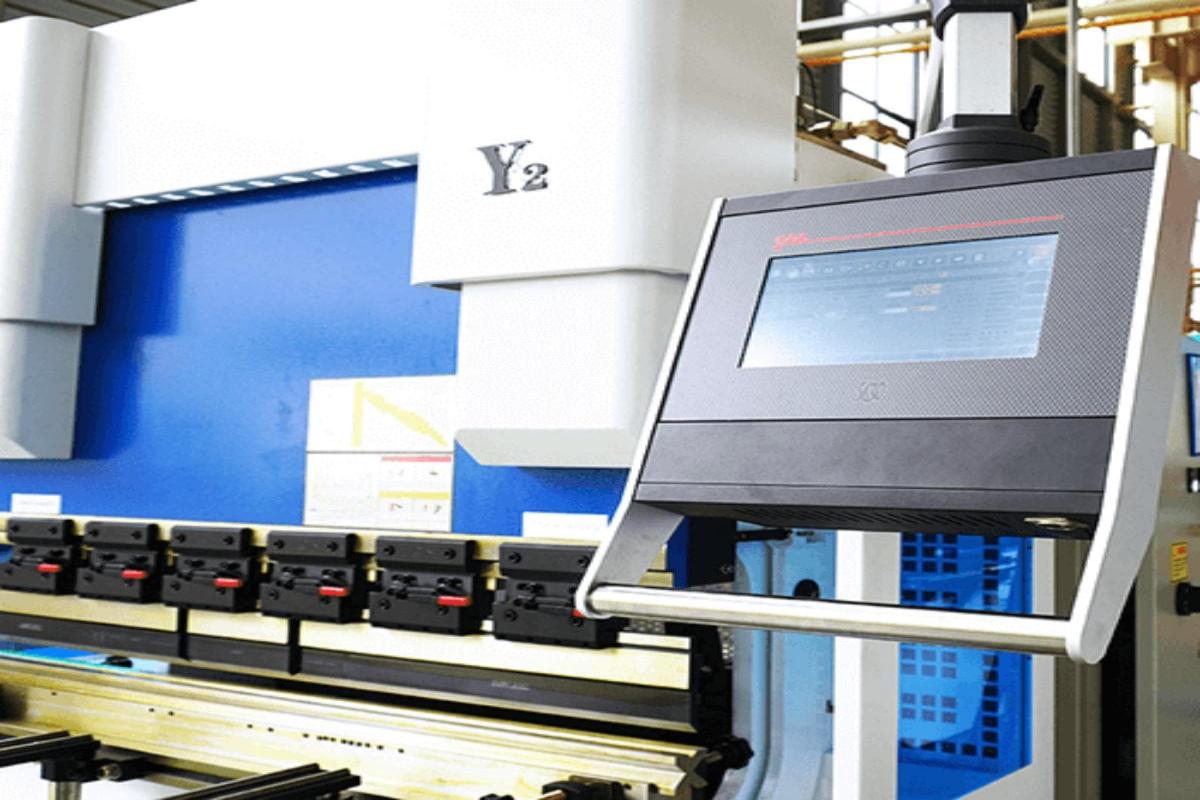
2. The hydraulic press brake ram is not vertical when running
The wear and tear of the guide rail and inadequate lubrication over time can lead to increased clearance. It is essential to inspect the degree of wear on the guide rail and adjust the clearance accordingly.
If the wear is significant, the guide rail plate needs to be replaced. Failure to lubricate the press brake on time can exacerbate friction between moving parts. To prevent untimely lubrication, it is recommended to use an automatic or semi-automatic lubrication system.
To ensure the longevity of the press brake, it is best to choose a tin bronze plate or ductile iron with a joint surface that is ground. The connecting bolt should be positioned below the joint surface and have a serrated lubricating oil groove to promote efficient lubrication.
3. Ram upset
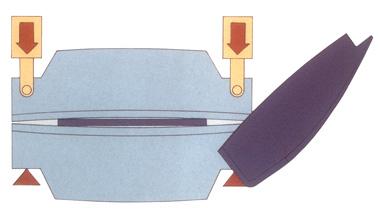
Long-term bending can cause the hydraulic press brake ram and the center of the worktable to bulge. This protrusion, known as deflection, refers to the upward protrusion of the ram and downward bending of the center of the worktable under maximum tonnage load.
Deflection is limited by the maximum tonnage load, and the ram and worktable can return to their normal positions if the load is removed. However, if the ram and worktable are defective and the tonnage load is too high, it may cause temporary or permanent damage to the center of the ram and worktable.
This results in a larger distance between the center of the ram and base compared to the distance at both ends, causing the angle of bending at the center to be greater than the angle of bending at both ends. This defect can impact the accuracy of bent workpieces and result in a canoe-like shape.
To mitigate this issue, it is recommended to gradually adjust the load within the machine's flow rate tonnage range, equip the machine with a crowning device, and use shims to offset the deflection of the ram. If compensation is no longer possible, the only solution is to remachine the ram and worktable.
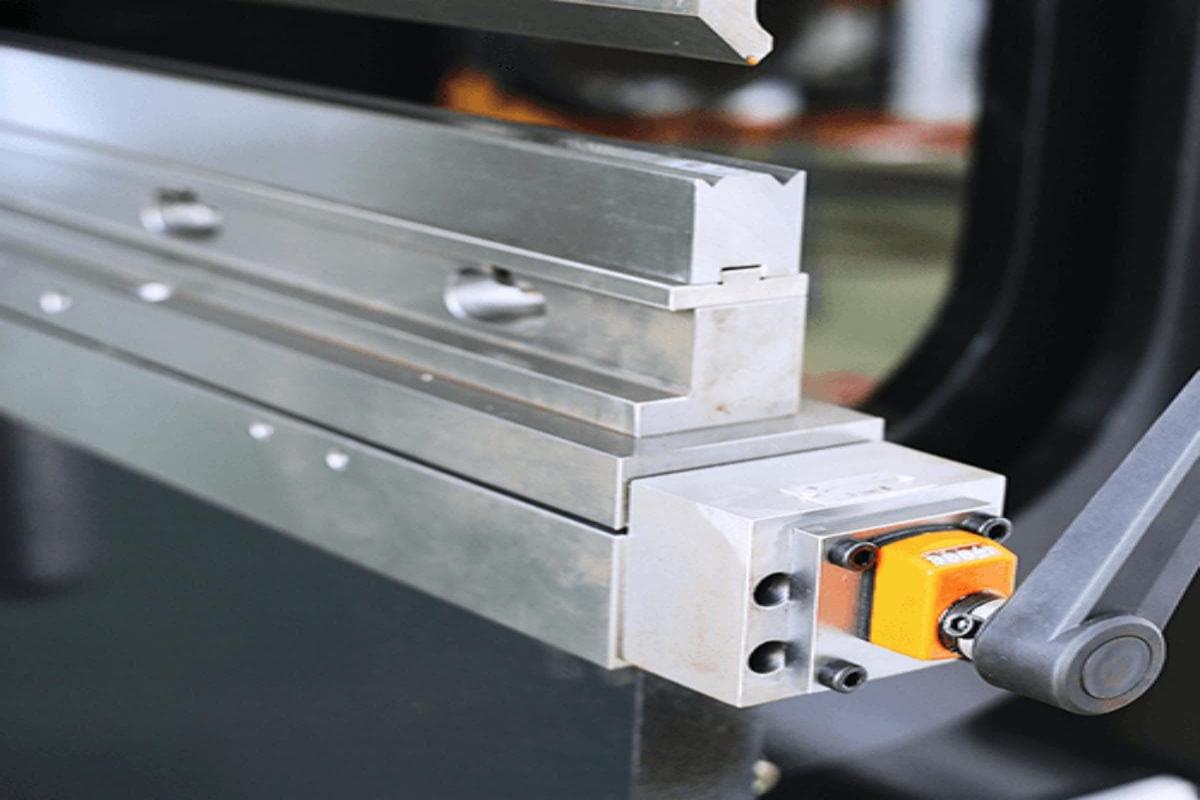
4. The ram cannot move down quickly / slowly
If the ram's movement is too slow when it moves down, it may be due to the tightness of the guide rail or a lack of signal from the servo proportional valve. Another possible cause is that each axis of the back gauge is not properly adjusted. Check the timing belt and servo motor for wear or malfunctions that might affect the backgauge axis performance.
Additionally, the ram may not return to the top position due to a stuck filling valve or a leaky sealing ring. To troubleshoot this issue, it is important to check the appropriate tightness of the ram guide rail and to ensure that the electromagnetic proportional directional valve has an electric signal.
Additionally, the axis of the back gauge should be checked to ensure it is in place according to the controller's programming. Check whether the filling valve is stuck and the sealing ring is leaking. If so, please clean the filling valve and reinstall it to make the valve core flexible.

5. Incorrect bending radius
An incorrect bending radius can cause damage to tooling and result in inaccurate bending of the workpiece. This can occur when the bending radius is too small and the common hydraulic pressure on the die tip becomes excessive, or when the opening of the workpiece is too close to the bending radius.
To avoid damage to the tooling and workpiece, the following measures should be taken:
- Determining the bending radius based on the material specifications for each process.
- Understanding that the bending radius for longitudinal bending is larger, while the bending radius for transverse bending is smaller.
- Ensuring that the distance between the plate opening (such as a notch) and the bending line is at least three times the thickness of the plate to prevent deformation of the workpiece.
Different materials have varying degrees of ductility and tensile strength, so it is important to consider these factors when determining the bending radius.
6. The main motor cannot be started
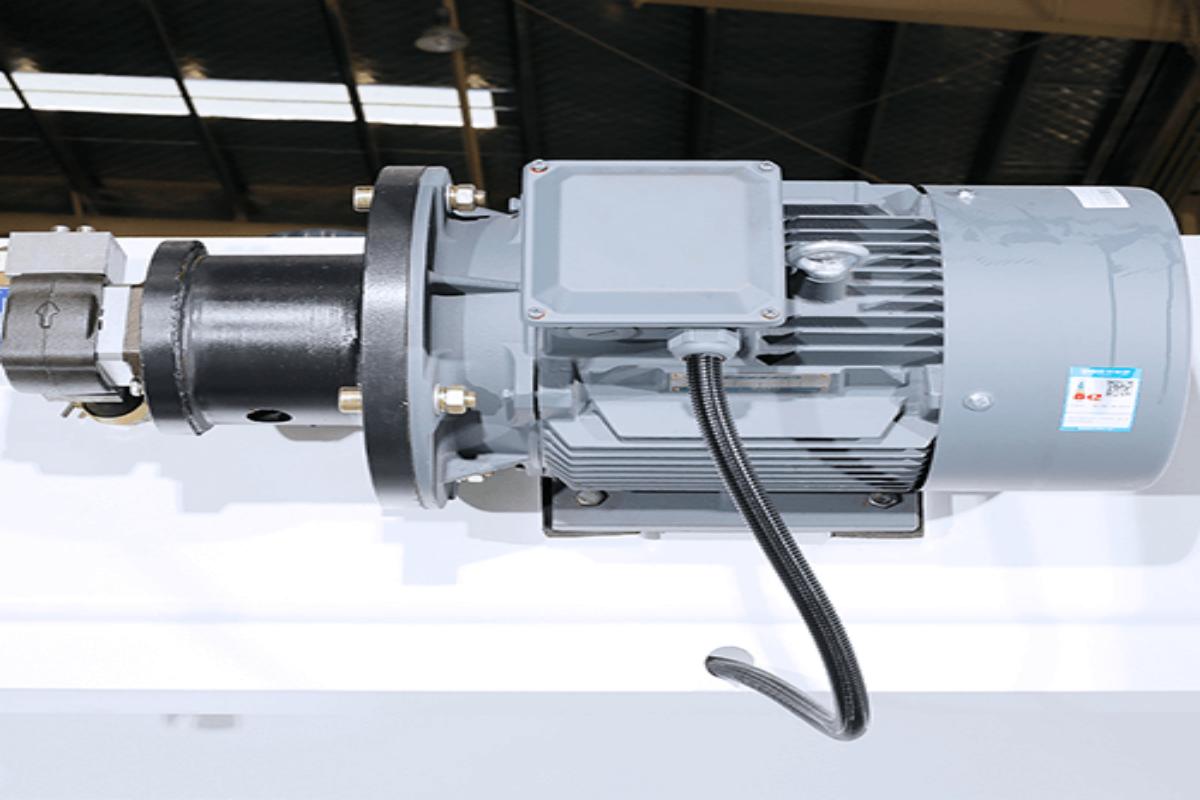
The failure of the main motor can be caused by loose wiring or a faulty control power supply. Additionally, it is important to ensure that the emergency stop button has not been engaged.
Other potential causes include damage to the AC contactor, circuit overload, or a faulty thermal relay.
To troubleshoot this issue, check the wiring of the switch power supply, verify that the emergency stop button has been released, and ensure that there is adequate overload protection in the circuit. Additionally, inspect other parts for damage.
7. The workpiece is cracked after bending and uneven bending
After bending, cracks may appear on the surface of the workpiece. This can be due to a small inner bending radius of the die or a small bending gap. The material itself may also be defective, with burrs facing outwards.
The curved end of the workpiece may also become uneven, which is due to the shrinkage and deformation of the outer surface after stretching, and the folding and deformation of the inner surface after compression.
To remedy these issues, it is necessary to improve the smoothness of the tools and increase the bending radius of the die. Adjusting the bending gap and using metal materials with better plasticity can also help. Ensure that the fillet radius of the die corresponds to the external fillet of the part.
Select appropriate materials, ensuring they are suitable for the bending process and within their recommended tensile strength. Adjust tooling, reduce stress concentration on the material. Use Proper Lubrication:Â This can help by reducing friction and stress during bending.
8. The hydraulic system has no bending pressure
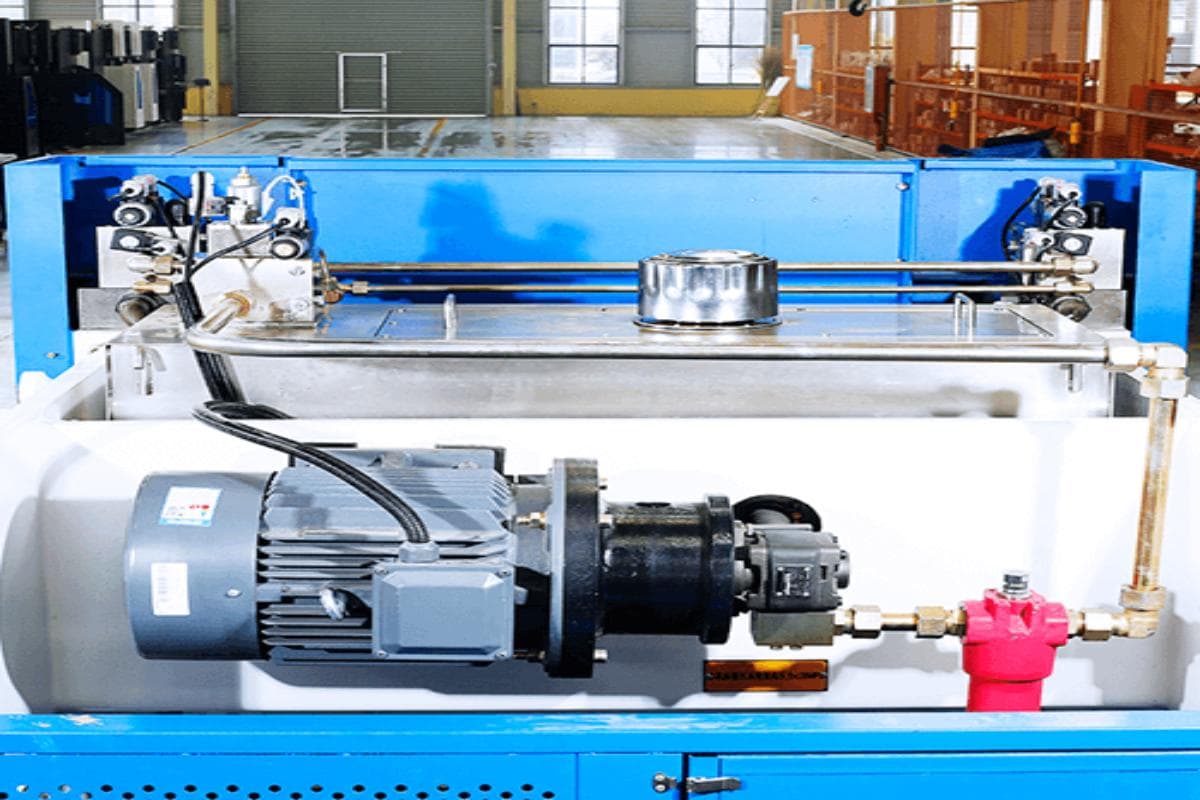
The cause may be due to blockages in the throttle hole and valve element or a leak in the piston sealing ring of the cylinder. To resolve this issue, check if the throttle valve and valve element are blocked and clean any blockages promptly.
Ensure that the filling port of the oil tank is filled with hydraulic oil and that the tank is completely filled to vent any gas. Inspect the piston sealing ring for leaks and replace it as needed.
III. Troubleshooting Checklist for Common Press Brake Problems
Problem | Checklist |
UnevenBending | - Check if the punch and die are aligned. - Inspect the punch and die for wear or damage. - Ensure the material is correctly positioned against the back gauge. -Verify the press brake alignment to ensure there is no offset. -Calibrate the machine to ensure accurate settings. |
Springback | - Check if the bend angle is appropriately increased to compensate for springback. - Ensure the inside bend radius is small enough. - Consider heat treating the material to reduce springback. Â - Verify that the material used is suitable for bending and has low springback characteristics. |
Over-bending or Under-bending | - Calibrate the press brake settings to ensure accuracy. - Check if the tooling and material thickness are appropriate for the desired bend. - Regularly inspect and maintain the tooling to prevent wear. |
Cracking | - Ensure the material used is suitable for bending and within its recommended tensile strength. - Adjust the tooling to reduce stress concentration on the material. - Use proper lubrication to reduce friction and stress during bending. - Consider pre-treating the material to improve its ductility. |
Surface Imperfections | - Use softer tooling or protective layers on the tooling surfaces. Â - Regularly clean the tooling to remove any debris or contaminants that could cause scratches or dents. - Inspect the tooling for damage and replace it as necessary. |
Wrinkling or Folding | - Adjust the punch and die clearance to ensure it is suitable for the material thickness. - Use appropriate tooling to provide adequate support to the material during bending. Â - Ensure proper material support using back gauges or support arms. |
Back Gauge Inaccuracy | - Regularly calibrate and maintain the back gauge to ensure it is functioning correctly. - Verify the sensors and mechanical components for accuracy and replace any faulty parts. - Use advanced backgauge systems with programmable settings to improve precision. |
Tool Chipping or Breakage | - Use high-quality toling that is appropriate for the material being bent. - Regularly inspect the tooling for signs of wear or damage and repair or replace it promptly. - Properly maintain the tooling and use the correct settings for the material. |
IV. Conclusion
We have discussed some press brake bending problems and press brake troubleshooting common solutions. Many issues can arise with press brake machines, and not all of them can be listed here. If you require further information, please feel free to contact us for more detailed answers.Â
My company, ADH Machine Tool is a professional sheet metal manufacturer that has produced hydraulic press brakes, shears, and fiber laser cutting machines for over 40 years. Proper maintenance is crucial for a press brake's efficient use and prolonged service life.
Automatic Quilting Sewing Machine
Cost-effective High-quality Sewing Machines,OEM-ready of Equipment,Clothing Production Machines
Sichuan Kisae sewing machine Co.,Ltd. , https://www.kisaesew.com