I. What Is A Punch Press
A punch press machine is used in conducting the punching process. Given the very nature of the said process, this machine is truly designed to alter the size or shape of a material by applying pressure to a tool, called a die, into the workpiece that is being held against it. The size or shape that will be produced on the workpiece is determined by the size or shape of the die.
As mentioned, the die determines the size of the shape of the workpiece. Hence, it is usually clamped onto a bed or anvil, making it perpendicular to the path of the ram. The punch, on the other hand, is attached to the accompanying hydraulic-powered ram of the punch press machine.
Punching is one of the many forming processes used in sheet metal manufacturing. The process involves pressing a workpiece through a die to change its shape and size, which is determined by the tooling used.
Punching is mainly used for sheet metal processing and can perform actions such as punching, perforating, piercing, and slotting. Small punches can be manually operated, while larger punches are typically controlled by CNC.
Small punches are suitable for batch production of small, uniform parts. The die size of larger punches is larger and more complex and often has a multi-station turret. The ram moves the punch up and down, pressing it into the die to perform the punching, perforating, and slotting.
Materials that can be processed by a punch press include cold-rolled steel, aluminum, and bronze. There are two main types of frames for a punch press machine: the C-frame, also known as a "door" frame, and the gantry frame.
In a C-frame punch, the hydraulic cylinder is located on the beam and connected to the ram, driving it. The bottom plate of the C-frame uses T-bolts to lock the mold support. The top and bottom of the punch are connected by a supporting strut and bushing assembly.
In a gantry frame, the oil cylinder is installed in the center of the machine to prevent deflection and deformation. To date, there are two common types of punch press machines that manufacturers can use.
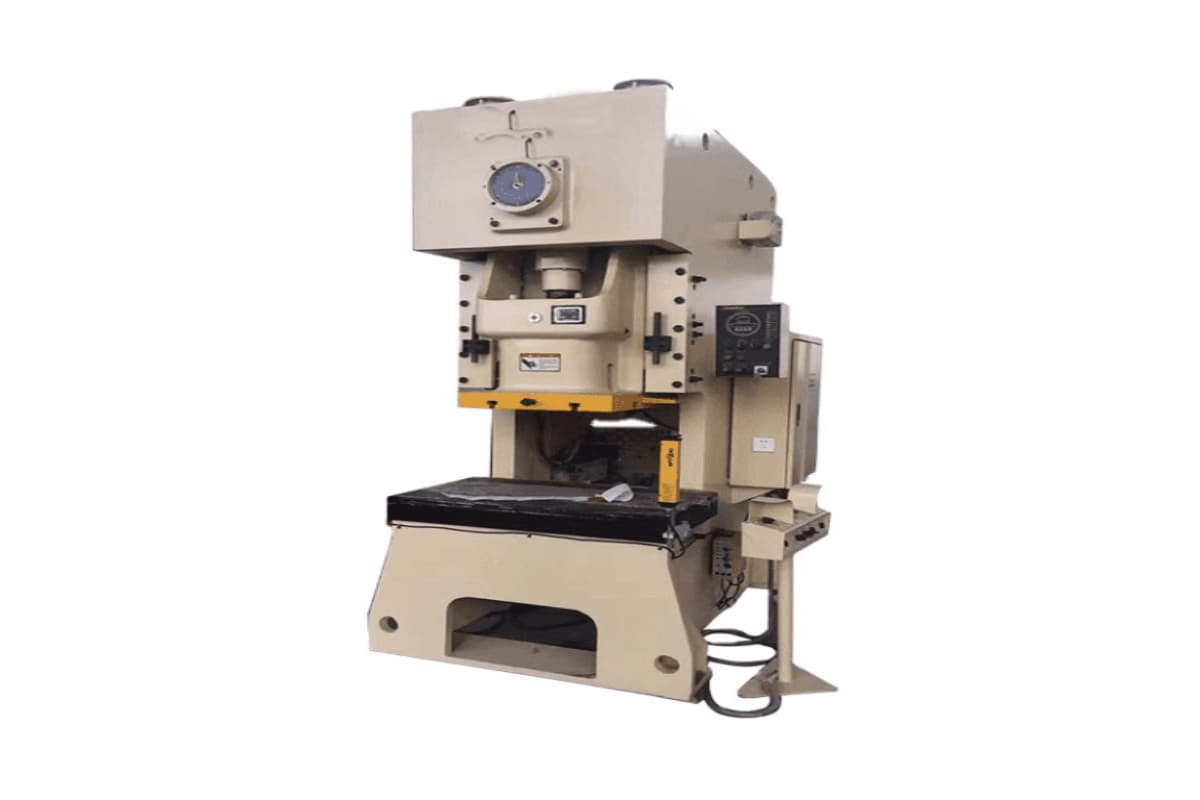
1. What is a mechanical punch press?
Mechanical punch presses are usually classified into two types, depending on the type of clutch or braking system with which they are equipped: full rotary and partial rotary, based on their braking and clutch systems.
Full revolution punch press machines have a crankshaft that rotates fully, which makes it dangerous as it can stop the machine at any moment. In contrast, partial rotary punch presses are equipped with rotary clutches and brakes, making it possible to safely stop the machine.
2. What is a hydraulic punch press?
In today's world of manufacturing technology, a hydraulic punch press is a type of machine that powers the ram with a hydraulic cylinder rather than a flywheel, which exerts immense pressure on the metal.
The stroke of the hydraulic punch press is regulated by a feedback valve, leading to an increase in the accuracy of the hydraulic ram movement and improved punching precision.
II. Parts of Punch Press
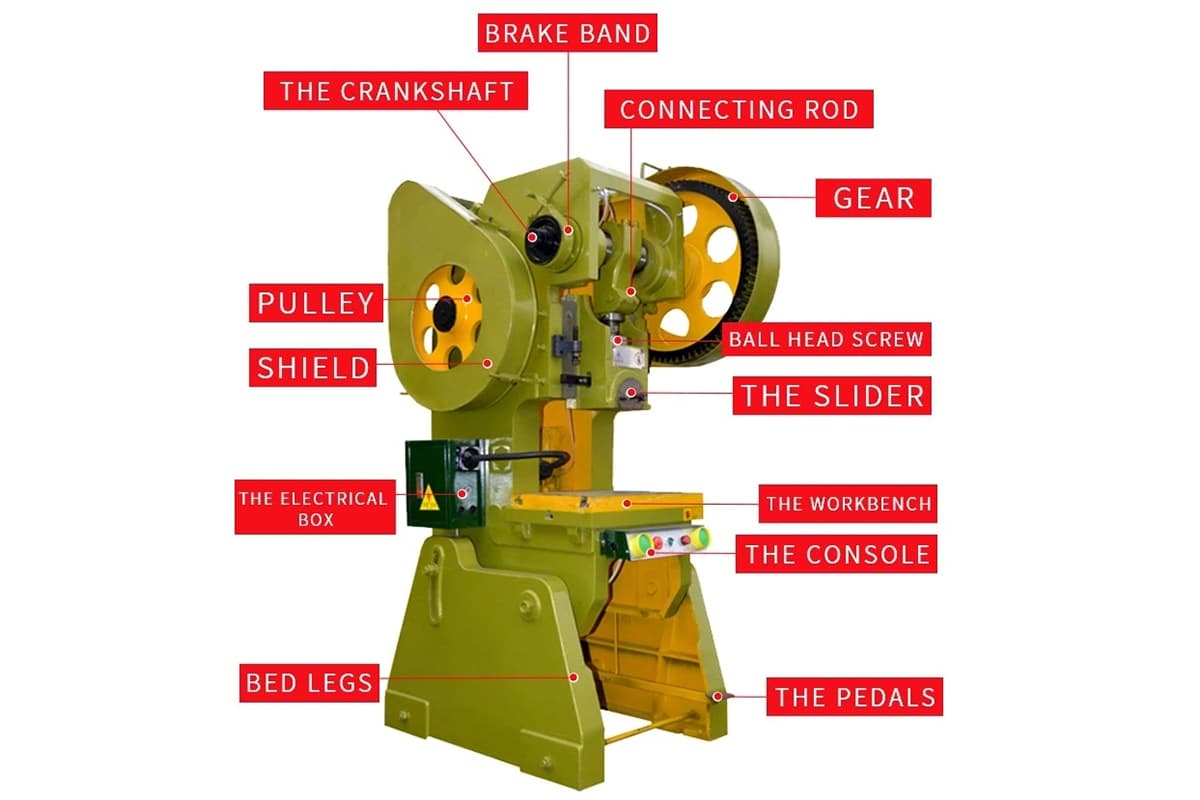
1. Frame and worktable
The frame of the punch press is the external structure that supports the entire machine. It houses the control and drives systems of the punch press. The worktable, located below the frame, provides a base for holding the die and workpiece in place.
The size of the worktable determines the maximum size of workpiece that can be processed. The beam, located at the upper part of the frame, houses the driving device, such as the hydraulic system.
2. Ram
The ram is the component of the punch press that drives the punch to process the workpiece under pressure. It is connected to the power system and its up-and-down movement is limited to a fixed stroke and strength. The stroke, refers to the up and down movement of the ram, and the speed can be adjusted as needed.
3. Connecting rod
The connecting rod is the part that connects the ram to the crankshaft. It plays a crucial role in transmitting the power from the ram to the punch.
4. Flywheel
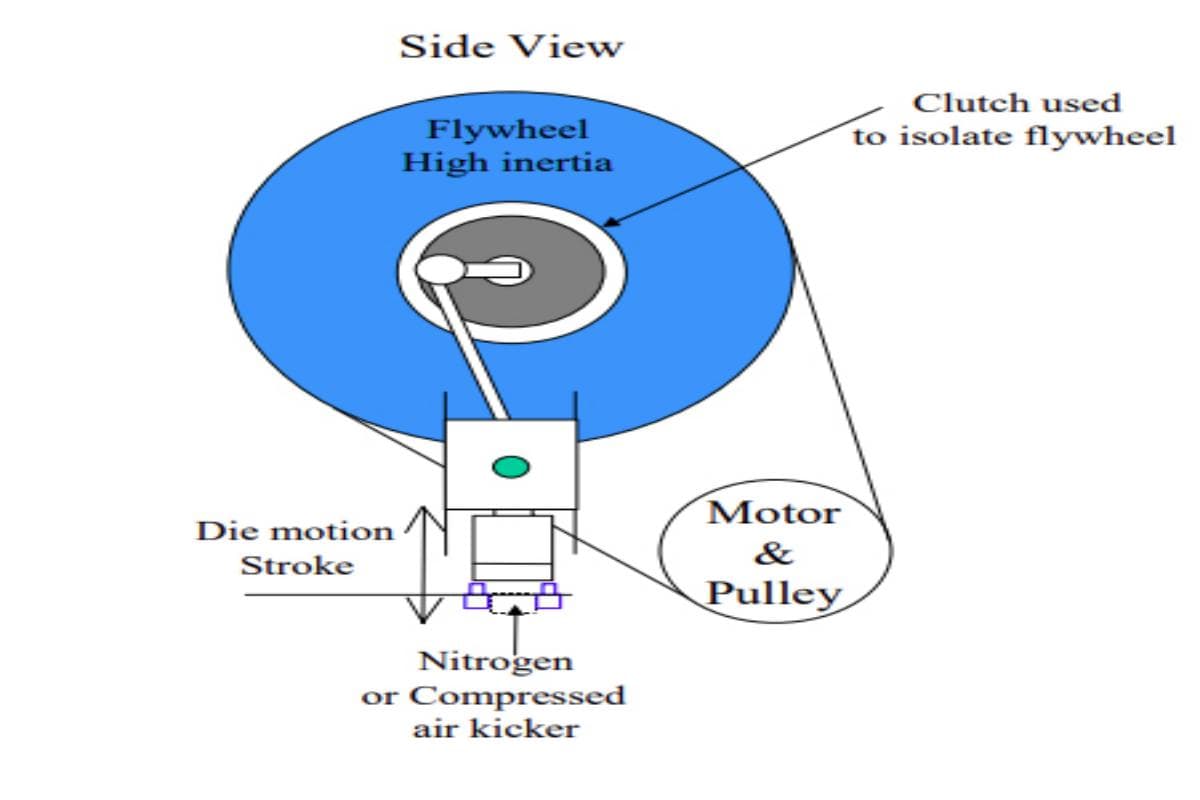
Most punch presses are now hydraulically powered for convenience, but previously, a constantly rotating flywheel would provide power to the ram. The flywheel is a high-inertia rotating body that is utilized to store energy provided by the drive motor. It stores energy to maintain the steady speed of the ram.
A flywheel is attached to the drive shaft, storing energy when the machine is idle in between cuts and delivering it to the shaft during punching. The flywheel prevents rapid or sudden changes in speed during the punching cycle.
Punch presses are usually driven by electric motors where the power demands are intermittent. During the non-working part of the punching cycle, the motor recharges the energy released during punching back into the flywheel.
5. Drive and control mechanism
The crankshaft and eccentric mechanism are powered by the motor to drive the ram. A control mechanism is utilized to regulate the length and power of the ram's stroke. Today, with the advancement in automatic control technology, the stroke of the ram can be controlled with greater accuracy.
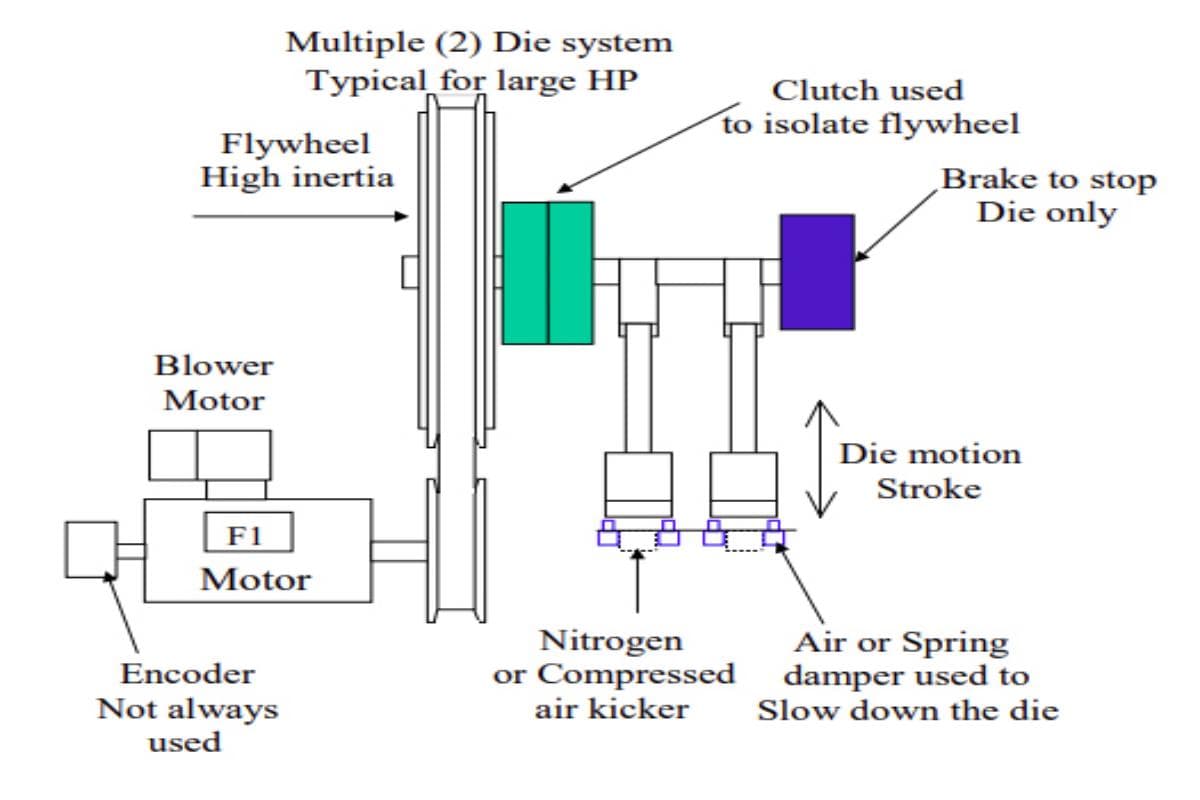
6. Punch and die set
The punch is a crucial component of the punch press, and it primarily processes the workpiece through the die. The die is mainly utilized for cutting, punching, piercing, and forming workpieces. A complete set of tool combinations includes both the upper die and the lower die.
The workpiece is placed on the lower die, and the punch is then pressed into it to create a hole in the workpiece. A punch press is a large piece of machinery featuring a hydraulic-powered ram at the top and operated by manufacturers that have the capability of punching holes at high speed.
7. Brakes
The brake system of the press machine is crucial for its safe operation. It disconnects the drive shaft from the flywheel, effectively stopping the machine. There is also an emergency brake located at the base of the machine that can quickly cut off power.
III. Features of Punch Press
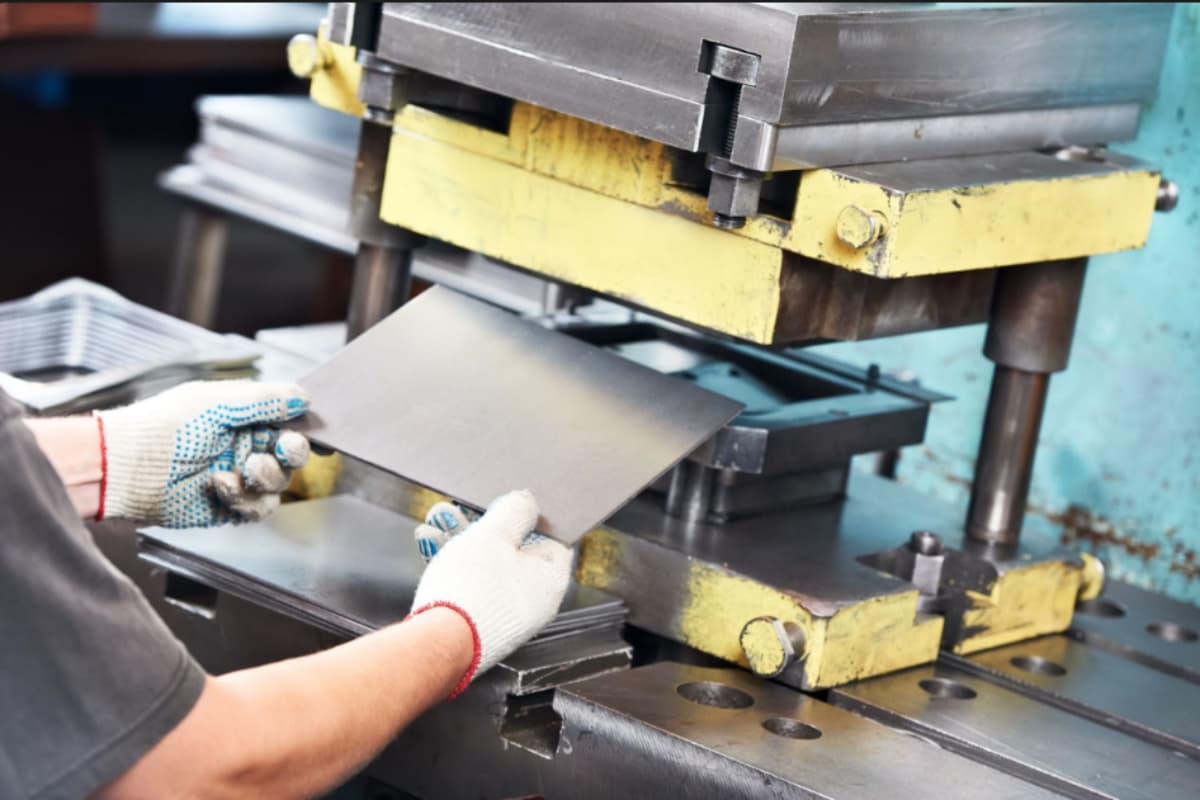
The components of the press machine, including the crankshaft, gear, and transmission shaft, are hardened and heat-treated after grinding, resulting in high resistance to wear. This enhances the stability of the machine's performance and the accuracy of its operation.
The frame of the machine is welded using a steel plate and has high rigidity and accuracy. After undergoing heat treatment, the frame is stable, with uniform load distribution across each component and balanced rigidity.
The press brake is highly sensitive and features a double electromagnetic control valve and an overload protection device. This ensures that the ram and punch can move and stop accurately and safely.
The automatic feeding system allows for fully automated production, increasing efficiency and reducing cost. It includes error detection, pre-cutting, and pre-breaking devices and enables quick and safe manual and electrical adjustments to the ram with high accuracy and convenience.
IV. How does A Punch Press Work?
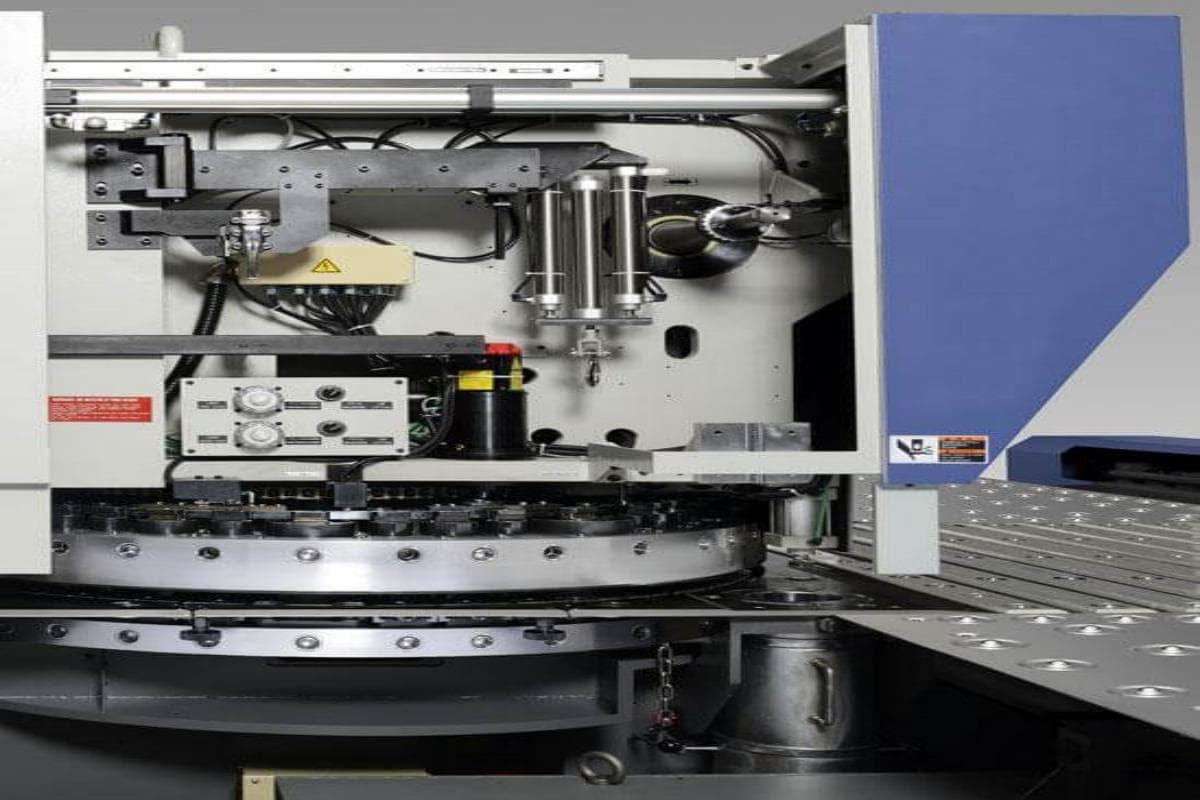
The punch press is powered by a motor and its operation is driven by the main motor that drives the flywheel. The connecting rod and clutch are attached to the crankshaft and the flywheel's motion drives the crankshaft.
This results in the entire drive system causing the ram to move up and down and converting rotary motion into linear motion. Punches are attached to the ram and the die is installed on the base.
During operation, the punch moves vertically downwards, punching a hole into the material and entering the lower die. The resulting blank is then used for further processing of the workpiece. CNC punch presses are controlled by a computer and primarily used to control the punching process.
V. Advanced Control Systems in Punch Presses
Modern punch presses are equipped with sophisticated control systems that enhance precision, efficiency, and ease of operation. These systems often include CNC (Computer Numerical Control) technology, which allows for precise control over the punching process. CNC systems can store multiple programs, enabling quick changeovers and reducing setup times. This is particularly beneficial in high-mix, low-volume production environments where flexibility is key.
For instance, a CNC operated punch press can automatically adjust the position and angle of the workpiece, ensuring consistent quality across different batches. The integration of servo-electric technology further improves control by providing precise, repeatable movements. Servo-electric drives offer better energy efficiency compared to traditional hydraulic systems, as they only consume power when in motion.
Additionally, modern punch presses may feature automated tool changers, which can significantly reduce downtime. These systems can quickly swap out tools based on the programmed requirements, allowing for seamless transitions between different punching operations. This automation not only speeds up the production process but also minimizes the risk of human error.
VI. Maintenance and Upkeep of Punch Presses
Maintaining a punch press is crucial to ensure its longevity and optimal performance. Regular maintenance routines should include both preventive and corrective measures. Preventive maintenance involves scheduled inspections and servicing to prevent potential issues before they arise. This can include checking and lubricating moving parts, inspecting electrical connections, and ensuring that all safety mechanisms are functioning correctly.
For example, hydraulic punch presses require regular monitoring of hydraulic fluid levels and quality. Contaminated or low hydraulic fluid can lead to decreased performance and potential damage to the system. Filters should be replaced periodically to maintain fluid cleanliness. Additionally, the hydraulic circuit, including pumps, valves, and cylinders, should be inspected for leaks or wear.
In contrast, servo-electric punch presses have fewer maintenance requirements due to the absence of hydraulic components. However, it is still essential to regularly check the condition of the servo motors and drives. Ensuring that the electrical connections are secure and free from corrosion is also vital.
Corrective maintenance involves addressing any issues that arise during operation. This can include replacing worn-out tools, repairing damaged components, and recalibrating the control system. Modern punch presses often come with diagnostic software that can alert operators to potential problems, making it easier to perform timely repairs.
VII. What Is A Punch Press Used For
A punch press can improve efficiency, save energy, and reduce costs, and doesn't require highly skilled operators. The punch press can process a variety of workpieces through a range of tooling and techniques, including blanking, stamping, deep drawing, trimming, fine blanking, riveting, and extrusion. The workpieces produced using a punch press are used in a range of products such as aircraft, ships, computer cases, cabinets, sockets, and more.
1. Automotive Industry
In the automotive industry, precision and efficiency are paramount. A leading automotive manufacturer implemented a high-speed punch press to streamline the production of car body panels. The punch press, equipped with advanced CNC controls, allowed for rapid and precise punching of complex shapes and patterns. This not only reduced the cycle time but also minimized material waste. The integration of automated material handling systems further enhanced productivity by reducing manual intervention. As a result, the manufacturer achieved a significant reduction in production costs and an improvement in product quality, setting a new benchmark in the industry.
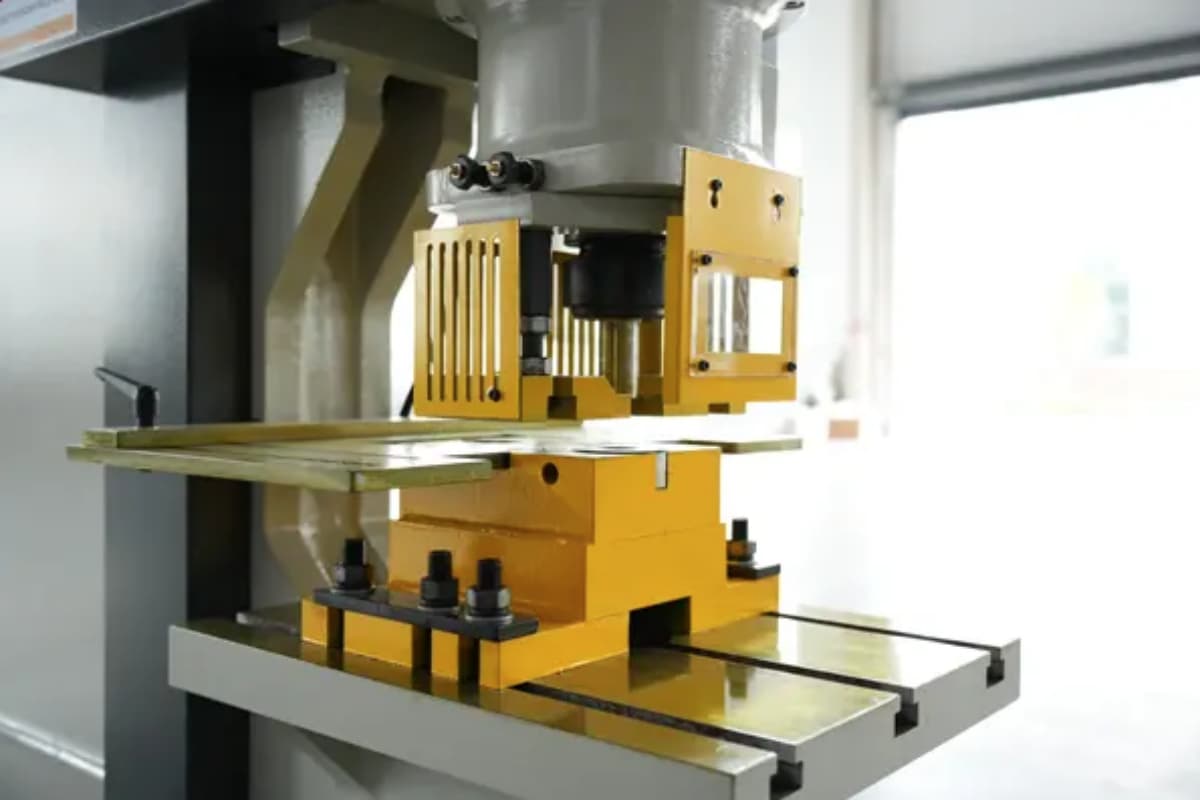
2. Electronics Manufacturing
Electronics manufacturing often requires the production of intricate and delicate components. A prominent electronics company adopted a servo-electric punch press to produce metal enclosures for their devices. The servo-electric technology provided superior control over the punching process, ensuring high precision and repeatability. The punch press was integrated with a robotic arm for automated loading and unloading of workpieces, which significantly reduced downtime. This setup enabled the company to meet the high demand for their products while maintaining stringent quality standards. The flexibility of the punch press also allowed for quick changeovers, accommodating various product designs with minimal setup time.
3. Aerospace Sector
The aerospace sector demands components that meet rigorous safety and performance standards. An aerospace parts supplier utilized a hydraulic punch press to manufacture structural components for aircraft. The punch press's high tonnage capacity allowed for the processing of thick and high-strength materials, essential for aerospace applications. The use of a hydraulic system provided the necessary force and precision to create complex geometries and tight tolerances. Additionally, the punch press was equipped with a tool monitoring system to ensure consistent quality and prevent tool wear. This implementation not only enhanced the supplier's production capabilities but also ensured compliance with the stringent requirements of the aerospace industry.
4. Construction Equipment Manufacturing
Manufacturers of construction equipment often deal with large and heavy workpieces. A construction equipment manufacturer employed a tandem punch press system to produce chassis components for their machinery. The tandem setup, consisting of two synchronized punch presses, allowed for the simultaneous processing of large metal sheets, significantly increasing throughput. The punch presses were integrated with a conveyor system for efficient material handling, reducing the need for manual labor and minimizing the risk of workplace injuries. This approach enabled the manufacturer to meet the growing demand for their equipment while maintaining high standards of safety and efficiency.
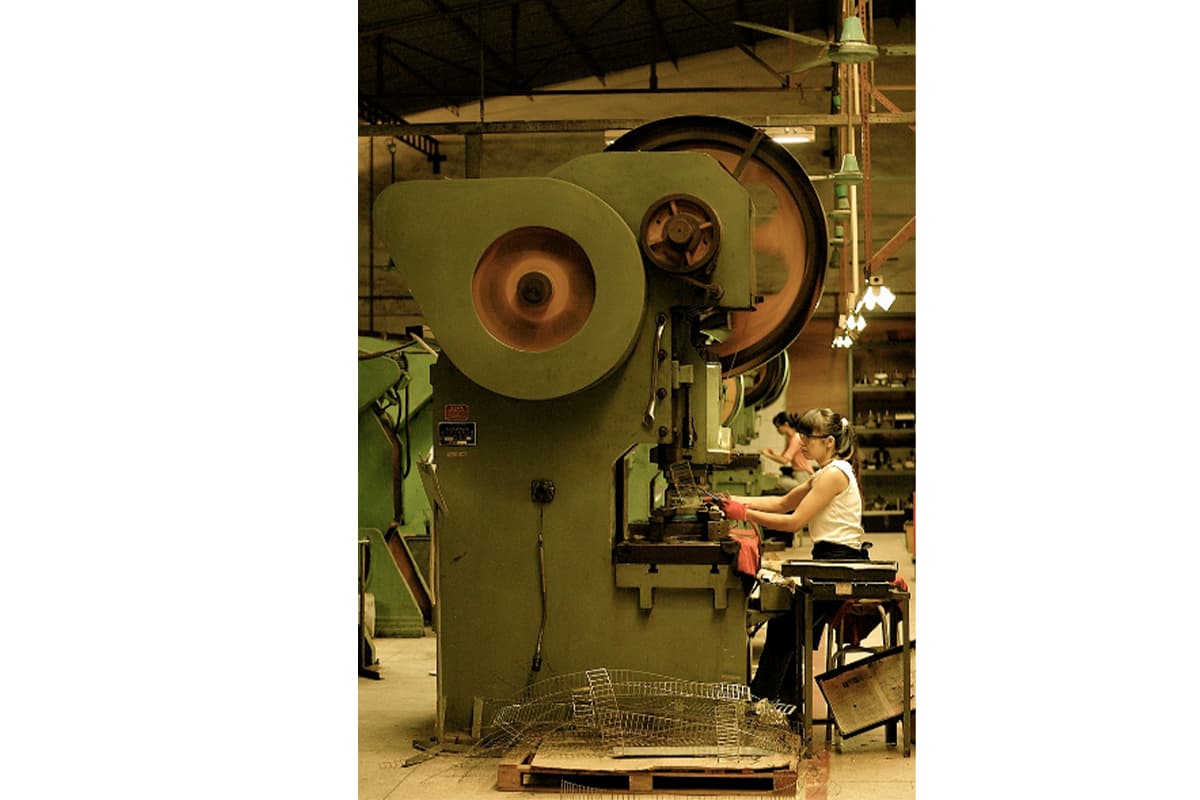
5. Consumer Goods Production
In the consumer goods sector, speed and versatility are crucial. A leading producer of kitchen appliances implemented a turret punch press to manufacture metal parts for their products. The servo drive turret punch press, with its multiple tool stations, allowed for rapid tool changes and the production of various part geometries in a single setup. The integration of a CAD/CAM system streamlined the design-to-production process, enabling quick adjustments to product designs. This flexibility allowed the company to respond swiftly to market trends and customer demands, maintaining a competitive edge in the fast-paced consumer goods market.
VIII. Conclusion
In this article, we have discussed a punch press's definition, composition, characteristics, application, working principle, etc. By now, you should have a good understanding of the punch press and its various components.
Punch presses are one of the essential pieces of equipment in the metal fabrication industry. Whether it's a C-frame or a portal frame punch press, they can efficiently perform various processing tasks such as punching and cutting. Mechanical and hydraulic punch presses each have their advantages and can be selected according to specific production requirements. With the continuous advancement of technology, the application of CNC punch presses is becoming more and more widespread, greatly improving production efficiency and processing accuracy.
As a metal processing equipment manufacturer with more than 40 years of experience, ADH Machine Tool is always committed to providing customers with high-quality and high-performance products such as press brakes, shears, and laser cutting machines. If you are interested in our products and services, please feel free to contact us at any time. Our professional team will be dedicated to serving you.Â
Gridwall Panel With Accessory,Retail Shelving Units,Grocery Store Shelves,Retail Display Racks
Suzhou Aomeijia Metalic Products Co,Ltd. , https://www.amjshelf.com