I. Introduction
In the world of metal fabrication, precision is paramount. Whether you're working with simple cold-rolled steel or exotic alloys, understanding and accurately calculating bend allowance is crucial to achieving the desired results and understanding how sheet metal parts are fabricated.
Bend allowance is not just a theoretical concept; it plays a vital role in ensuring that the final product meets the exact specifications required for its application in precision sheet metal fabrication.
1. Background of Bend Allowance
Bend allowance refers to the amount of material that needs to be added or subtracted from the flat pattern to achieve the desired bend. This calculation takes into account the stretching and compressing of the material that occurs during the bending process.
The concept of bend allowance has been a cornerstone of metalworking for decades, evolving with advancements in materials and bending technologies. Historically, fabricators relied on empirical data and experience to estimate bend allowance.
However, with the advent of computer-aided design (CAD) and computer-aided manufacturing (CAM) systems, the process has become more precise and data-driven. Modern fabrication shops use sophisticated software to calculate bend allowance, considering factors such as material type, thickness, bend angle, bend radius, and inside radius.
2. Importance of Bend Allowance in Production
The importance of bend allowance cannot be overstated. Accurate bend allowance calculations ensure that the final product dimensions are precise, which is critical for parts that need to fit together seamlessly in assemblies. Incorrect bend allowance can lead to parts that are either too short or too long, resulting in costly rework or scrap.
(1) Case Study: High-Precision Aerospace Components
Consider the aerospace industry, where components must meet stringent tolerances to ensure safety and performance. A leading aerospace manufacturer needed to produce a series of complex brackets with multiple bends. Each bracket had to fit precisely within the aircraft's fuselage, with no room for error. By using advanced bend allowance calculations, the manufacturer was able to produce brackets that met the exact specifications, reducing waste and ensuring the structural integrity of the aircraft.
(2) Case Study: Heavy-Duty Construction Equipment
In another example, a company specializing in heavy-duty construction equipment faced challenges in bending thick steel plates for excavator arms. These components required precise bends to ensure proper function and durability. The company implemented a detailed bend allowance calculation process, which included material testing and software simulations. This approach allowed them to produce components that met the high standards required for heavy-duty applications, minimizing downtime and maintenance costs.
3. Practical Applications of Bend Allowance
Bend allowance is used in various industries, each with its unique requirements and challenges. Here are a few practical applications:
- Automotive Industry: In the automotive sector, bend allowance is critical for producing components such as chassis parts, brackets, and exhaust systems. Accurate calculations ensure that these parts fit together correctly, contributing to the overall safety and performance of the vehicle.
- Construction Industry: For construction equipment, precise bend allowance calculations are essential for producing structural components that can withstand heavy loads and harsh conditions. This includes beams, supports, and frames used in buildings and infrastructure projects.
- Consumer Electronics: In the consumer electronics industry, bend allowance is used to create enclosures and frames for devices such as smartphones, laptops, and tablets. These components require high precision to ensure proper assembly and functionality.
- Medical Devices: Medical device manufacturers rely on accurate bend allowance calculations to produce components such as surgical instruments and implants. These parts must meet strict regulatory standards and perform reliably in critical applications.
II. What Is Bend Allowance?
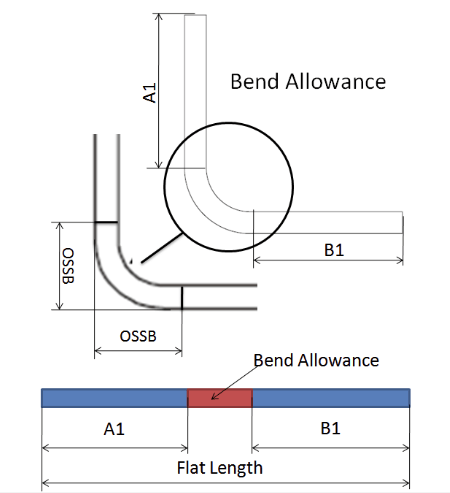
Bend allowance is an important factor in achieving accurate results in press brake bending. The metal sheet undergoes stretching on the outside and compression on the inside due to the forces of tension and pressure during the bending process.
Therefore, it is necessary to consider both bend allowance and bend deduction in the flat pattern of the workpiece to achieve the final accurate bending result. Both bend allowance and bend deduction are used in determining the dimensions of the flat workpiece drawing.
Bend allowance refers to the length of the neutral axis between the bend lines, and it is the length added to the flange length to get the bend allowance. The value of bend allowance is calculated as the difference between the total flat length and the total flange length of the workpiece in the flat pattern.
To calculate the bend allowance, the following parameters are needed: plate thickness, bending angle, internal radius, K factor, and others.
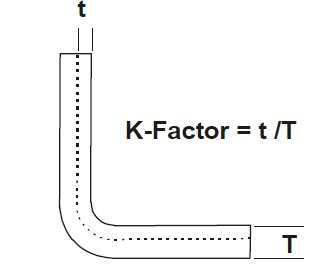
III. Bend Allowance Calculation
The bend allowance calculation formula is:

Where B is the bending angle, IR is the inner radius, MT is the thickness of the plate, and K is the K factor. The bend allowance formula takes into account the geometries of bending and the properties of your metal to determine the bend allowance.
The bend allowance calculator is:
Miño, L. Bend Allowance Calculator. Available at: https://www.omnicalculator.com/physics/bend-allowance. Accessed: Jun 19, 2024.This calculator works as a bend deduction calculator as well.
1. Thickness
Thickness refers to the thickness of the metal sheet and is a crucial parameter in the bending process. The thickness directly affects the bending force required and the calculation of bend allowance. Thicker sheets require more bending force and are more prone to spring back during bending. The thickness is usually measured in millimetres (mm) or inches (in), not by the gauge number.
2. Bend Angle
The bend angle refers to the angle formed by the metal sheet during the bending process. This angle determines the final shape and function of the product. The size of the bend angle affects the calculation of bend allowance because different angles result in varying degrees of stretching and compressing of the metal sheet. Common bend angles include 90°, 120°, etc.
You will determine the bend angle based on your part's complementary angle. Before calculating, it is important to convert from the included angle to the complimentary angle. The Inside Radius will be the finished radius of the included angle.
3. Inside Radius
The inside radius refers to the radius of the bend on the inner side of the metal sheet after bending. The size of the inside radius directly impacts the bend allowance because it determines how the metal flows and deforms during bending. A smaller inside radius results in greater material stretching and compressing, requiring more precise bend allowance calculations. The inside radius is usually denoted as R and measured in millimeters or inches.
4. K-Factor
The K-factor is a property of the material that you are bending, which can be used to describe the position of the neutral axis in the metal sheet during bending. The neutral axis is the layer that neither stretches nor compresses during bending. The K-factor typically ranges from 0 to 1, depending on the type and thickness of the material. The K-factor plays a crucial role in bend allowance calculations as it helps determine the actual length change of the material during bending.
5. Springback
Springback refers to the phenomenon where the metal sheet tries to return to its original shape after bending. This is due to the elastic recovery properties of the material. Springback affects the final bend angle, requiring multiple adjustments during the bending process to achieve the desired angle. The amount of springback depends on the type of material, thickness, and bend angle.
IV. Sheet Metal Bend Allowance Chart
The largest variations come from the materials themselves. Protective coatings, variations in the alloy and thickness, and many other small factors all add up to give you bend allowances that are unique to your operation.
This bend allowance chart will get you close enough for most applications and may not require fine-tuning. However, if you are truly dedicated to precise bending, download the excel chart and begin plugging in your own values.
The below Microsoft Excel chart is for even numbered gauges 8 through 24 and has a default K-Factor of .33 for each.
Calculation Example
Bend allowance is important because it gives us the information to cut sheet metal to produce a bent metal piece accurately. Let's walk through a real-world example to illustrate how to calculate the bend allowance.
(1) Example Parameters:
- Material: Mild Steel
- Thickness (T): 0.125 inches
- Inside Radius (R): 0.250 inches
- Bend Angle (A): 90 degrees
- K-Factor (K): 0.42
(2) Step-by-Step Calculation:
1. Convert Bend Angle to Radians:
2. Apply the Bend Allowance Formula:
Result:
The bend allowance for a 90-degree bend with a material thickness of 0.125 inches, an inside radius of 0.250 inches, and a K-factor of 0.42 is 0.475 inches.
V. Conclusion
The bend allowance and bend deduction are essential parameters for achieving accurate results in press brake bending. To obtain the correct dimensions of a flat workpiece drawing, both of these values must be taken into consideration.
The bend allowance refers to the length of the neutral axis between the bending lines, or in other words, the arc length of the bend, and is calculated as the difference between the total flat length and the total flange length of the workpiece in its flat pattern mode.
The bend deduction, on the other hand, is equal to the difference between the total flange length after bending and the total flat length. It is used to determine the flat pattern length of the sheet metal and the size of the workpiece.
When sheet metal goes through the bending process, the metal in the bend deforms and stretches. When this happens, your part's total length increases by a small amount. Likewise, when you're trying to develop the flat pattern, you have to subtract a portion from the desired part size to get the correct flat dimensions.
To calculate the sheet metal bend allowance, factors such as plate thickness, bending angle, internal radius, K factor, and others must be taken into account. The sheet metal bend deduction can be obtained once the bend allowance is known.
You can either use a formula or a bend allowance chart to calculate the bend allowance. For more information on bending and our press brake products, read our blog or contact our experts.
My company, ADH Machine Tool, not only offers press brakes but also panel benders, fiber laser cutting machines, shearing machines, and more. Our team of experts is available to help you with your needs.
Ribbed V Belt For Iveco Daily V,V Belt Ribbed For Iveco Daily V,Automotive Ribbed V Belt Iveco Daily V,Ribbed V Belt For Iveco
ZHEJIANG AOSITE AUTO PARTS CO.,LTD , https://www.aositebelt.com