Introduction
With the rapid development of computer technology and network technology, the real-time and correctness of information transmission has been greatly improved. The development of modern enterprises presents a trend of grouping and diversification. The distribution of enterprises' production, operations, and management is becoming wider and wider. The factory site spans different regions, and it is necessary to organize and manage production operations in a modern and effective manner. Share a large amount of information resources within the company. The development of electronic information technology (IT) has also greatly promoted the development of industrial automation technology. Industrial inspection and data communication, production process automation, and artificial intelligence technology have been widely used to form a comprehensive automated information system, which has further triggered the traditional industry. The technological progress has greatly improved the competitiveness of enterprises [1].
In the traditional sense, the power plant integrated automation system is mainly composed of the power plant's plant-level supervisory information system (SIS) and its connected lower-level field devices such as distributed control systems (DCS) and programmable logic controllers (PLCs). ) It is composed of smart meters. It monitors the operation of the entire power plant in real time and on-line management, including control, signal, measurement, protection, automatic devices and transmissions, etc. It utilizes computer technology and modern communication technology, through functional combination and optimized design. The implementation of automatic monitoring, measurement control and coordination of power plants is an integrated application of automation and computer and communication technologies in the power sector, which is of great significance for the safe and stable operation of power plants. However, it has the important defect of lack of communication and information sharing with the entire production decision.
The emergence of power plant management information system (MIS) is precisely to solve the problem of integration of production and decision-making information. It is used as the upper-level mechanism of SIS and DCS, and is based on DCS. It uses advanced technology for the purpose of economic operation and improvement of the overall efficiency of power generation enterprises. , Applicable, and effective professional calculation methods to realize information sharing and plant-level production process real-time information monitoring and scheduling throughout the power plant. It provides real-time, effective and reliable real-time operational data for decision-making of power plant management, and provides scientific and accurate economic indicators for companies operating under market conditions.
This article describes the experience of integrating power plant information integrated automation systems (hereafter abbreviated as IT systems) that integrates MIS with SIS and DCS technologies to achieve plant-wide information integration and sharing.
First, the basic structure and system of IT system
In the late 1980s, with the rapid development of computer technology and network technology, the combination of multiple technologies in the process industry enabled process control to break through the islanding model of automation, resulting in the integration of control, optimization, scheduling, management, and operations. The new integrated automation model, ERP/MES/PCS three-layer structure came into being [2]. In the three-tier structure, people hope to realize the comprehensive automation of the enterprise from the three aspects of business management, production management and process control, namely, to establish an enterprise resource planning (ERP) system and a manufacturing execution system (MES-manufacture). Execution system) and process control system (PCS). After the enterprise management decision-making level uses ERP to determine the enterprise product strategy and formulate an optimized production plan, the MES prepares production scheduling instructions from the production scheduling system (PSS) according to the company's equipment, raw materials, etc., and performs production scheduling (or units) for each production device. Optimize the calculation and give an optimized formula or production plan (setpoint) so that the DCS in the control domain can perform real-time operation and control of the underlying industrial production process according to the optimized formulation or production plan.
The key to the IT system is integration [3]. In the integrated system with MES as the core, a more meticulous 5-layer division is made, which is divided into 5 layers: decision-making layer, management layer, execution layer, process control layer, and support layer. , And 2 database systems (relational database systems and real-time database systems). The overall framework is shown in Figure 1.
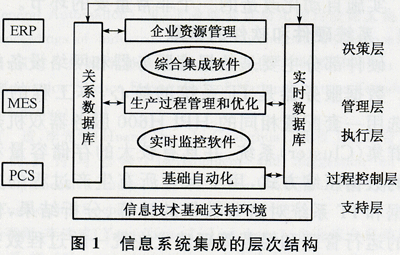
Among them: The decision-making layer includes the enterprise information portal, operation support decision-making, key business indicators and basic information; the management level includes production scheduling, workshop management, supply procurement, sales management, technology management, quality management, financial costs, measurement information, human resources , equipment management, energy management, safety and environmental protection; executive level includes real-time data monitoring, production scheduling, process simulation group, and optimization control; process control layer includes PLC control, DCS control, online quality inspection, data collection, security alarm, etc.; support layer Including information technology basic environment (network, computer equipment, system software, tool software). Wherein, the management layer extracts useful information from the relational database to help the decision, while the execution layer and the process control layer extract various information in the real-time production process from the real-time database to manage and monitor the normal operation of the production, of course, between the two. Data and information can also be exchanged and work together. It can be seen from the above hierarchical structure diagram that the functional modules of each level cooperate with each other and are closely linked together through interfaces to complete the information integration function.
Second, the implementation of IT systems
At present, many power plants have already equipped MIS and DCS equipment. The design of the IT system is based on computer and network technology, giving full play to the experience and creativity of all levels of management personnel, and optimizing the enterprise information resources by means of human-machine discussion [4], from operation, maintenance and operation On the one hand, it conducts decision-making consultation on the behavior of the electricity market in order to achieve integrated automation of information in power plants. The IT system made up for the shortcomings of MIS and DCS from aspects such as economic analysis and overall adjustment. It has become a bridge between MIS and DCS in terms of structure, and has made better use of the company's information to provide a favorable basis for production decisions.
The overall goal of the integrated management and control system for a 600MW unit in a Dingzhou Power Plant is to achieve economical operation of the unit on the basis of high-level unit-level unit control, and to gradually realize economic optimization scheduling and plant-wide economic optimization of the unit group. Management [5]. The system structure is shown in Figure 2.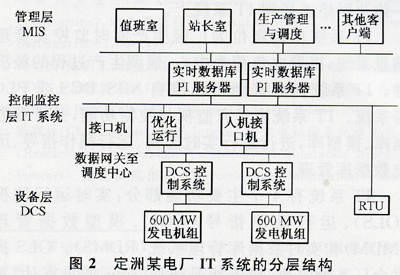
IT system uses client/server (C/S) architecture to complete various online monitoring functions of IT system control stations (such as unit performance calculation optimization analysis station, network system management and maintenance station, etc.), and can be seamlessly connected at the lower level of control Network and IT systems are redundant on industrial networks. The IT system real-time information data server provides centralized collection of information and system maintenance. The IT system provides a reliable firewall that protects the security of user information. Its rich and flexible client software package enables users to handle all of the maximum amount of production information in their hands. These client applications run under the familiar Windows and browser environment.
According to the principle of unified layout of the whole plant network, the design of network topology and equipment identification shall be carried out. The basic design principles are as follows: 1 1000Mbit/s fiber-optic Ethernet is used between each building group of the plant and the information backbone system; 100Mbit/s fiber-optic Ethernet is used between the control systems of the 2 floors and each unit; 3 the control of the main building The room is connected by l0Mbit.s-1/100Mbit.s-1 fiber optic Ethernet; 4 the office building and the main plant room are connected by Category 5 twisted-pair; 5 the backbone network adopts imported brand-name switches; 6 the work is taken between the outlets of the systems Group switch.
The advantages of adopting the integrated layout of the whole plant network system are: stable and reliable system; effective guarantee of network performance; easy maintenance and overhaul; easy upgrade and expansion;
The IT system uses a multi-layer C/S structure to minimize the communication conversion between systems. Balance data traffic between servers and different clients. The configuration principles are: 1 IT system interface station and DCS, PLC is connected in the form of a unified OPC server; 2 real-time data processing using high-performance redundant real-time data server; 3 application server to complete real-time tasks using industrial Ethernet and standard API interfaces and The control system is directly connected. Xinhua uses the load distribution station to directly connect to the control network of the DCS and also serves as a redundant site of the control system. 4 The relational database server interface through DBC and MIS; 5 The management application adopts the Web server method. Connection (optional); 6 All administrative clients are connected to the IT system through a factory-wide integrated network.
The IT system functions as a factory-level production real-time monitoring and management information system, focusing on the power generation load and emphasizing the economics of the production process. IT system information sources can be taken from systems such as MIS, DCS, or PLC. The IT system should have monitoring and control functions, with a database, a model library, and run real-time monitoring, operation and operation guidance, and historical database management.
The IT system has four main functional parts: OLS, OGI, Model Data Management (MDM) and Real-time Database Management System (RDMS). OLS provides plant-wide system monitoring, equipment condition assessment, and plant-wide energy auditing. It corresponds to DAS of DCS and realizes: 1Real-time information display of each thermal system of the whole plant; 2Generation of various required reports; 3Diagnostics of thermal system equipment failure , anticipation and defect management. OGI is based on the evaluation of operational economy, and proposes adjustment opinions due to operational parameter deviations, including load optimization allocation and operation optimization guidance, which is equivalent to MCS of DCS. MDM has data management functions for historical databases and calculation models, provides historical data query, supports modification of calculation model parameters, and is similar to the HSR function of DCS. The main function of RDMS is to store and manage real-time information at the production site, provide basis for enterprise decision-making and production scheduling, and also enable online inquiry to provide useful and real-time information and data for the first three functions.
Third, the key technologies
3.1 The use of real-time database
Since China's industrial companies currently implement the production process control and enterprise management information system in blocks, the system is completed after the two independent islands, there is a "slit" between the two, and the real-time database is An effective platform tool for filling "slits" between the two. The real-time database is the core of the plant-level monitoring information system[6]. Unlike Sybase and Oracle, the real-time database stores production data on a long-term basis in the prototype of the data, which can meet the requirements for fast and efficient data acquisition, storage, and display. The time accuracy of the saved data can reach microseconds. The real-time database is a standard C/S structure and has good openness and scalability. The scale is from 1000 points to several hundred thousand points. The structure is flexible and scalable. It supports multi-platform structure and multi-server structure. The significant difference between real-time databases and relational databases is that advanced data compression technology enables hundreds of thousands of points of production data to be stored on-line for a long period of time (at least for 3 years) with the data's original time and accuracy, which greatly reduces the Data storage space; Powerful data source interface functions (PI database has more than 300 interface functions), these interface functions ensure that the real-time database and most of the control system connection, to meet its wide range of application requirements. The realization of real-time database is an indispensable part of power plant IT system. It provides effective and timely data and information for management, decision-making, production, optimization and other institutions. It is a very important part of the automation transformation of power plants.
3.2 System Hardware and Software Selection
The hardware part is mainly the selection of database server and network equipment. The data server is the core of the IT system. The server of this project uses a dual-system hot-swap cluster system with the same HPL600 server configuration, and has a large storage capacity and advanced data compression methods to save all production processes. The real-time data and IT system's calculation and analysis results of these data make the whole plant's operation management and operation management based on the unified process data. In terms of network devices, the choice of core switches is mainly [7]. The core of the IT system is the redundantly configured 3Com high-performance Switch 4007 switch with high stability and scalability. Its 1000Mbit/s communication port can communicate with data collection switches and MISs for high-speed, large-volume data transmission. At the same time, the high-speed backplane bandwidth of the Switch 4007 supports multiple full-duplex 48 Gbit/s ports, enabling DCS, centralized water-ash control systems, remote terminal units (RTU), MIS, and other interface systems and servers for each unit. High-speed parallel communications. Through the 3Com 1000Mbit/s workgroup switch, each functional station in the IT system can quickly access the information of the real-time database.
The software mainly includes the software in the real-time database and the software in the MIS. The stable and reliable OSI real-time database PI of the US OSI is used as the core database of the real-time monitoring information system of a power plant in Dingzhou. OSI has made great efforts at the PI system client to make it fully compatible with the Windows 95/98 architecture, and its client products have been certified by Microsoft. In addition, the powerful standard application interface is also a major advantage of PI. In the MIS layer, according to the requirements of production management, maintenance management and equipment management, we use IFS/APPLICATION (enterprise asset management and maintenance and maintenance management system) and SAP software as the application software to realize the whole plant production management.
IV. Conclusion
After the implementation of the IT system, the operation was stable and the performance was good. It achieved the intended purpose and was recognized by the users. However, due to the high purchase price of PI series software, and many of these functions are not needed, we have developed and researched real-time database software. The currently-developed XSIS system has been able to replace PI to complete daily production and is already in Xingtai. The power plant is put into operation. It is not as powerful as the PI on the application interface. In terms of hardware, PC and PC servers can be used instead of dedicated database servers, which reduces the development of interface programs and reduces equipment costs.
With the rapid development of computer technology and network technology, the real-time and correctness of information transmission has been greatly improved. The development of modern enterprises presents a trend of grouping and diversification. The distribution of enterprises' production, operations, and management is becoming wider and wider. The factory site spans different regions, and it is necessary to organize and manage production operations in a modern and effective manner. Share a large amount of information resources within the company. The development of electronic information technology (IT) has also greatly promoted the development of industrial automation technology. Industrial inspection and data communication, production process automation, and artificial intelligence technology have been widely used to form a comprehensive automated information system, which has further triggered the traditional industry. The technological progress has greatly improved the competitiveness of enterprises [1].
In the traditional sense, the power plant integrated automation system is mainly composed of the power plant's plant-level supervisory information system (SIS) and its connected lower-level field devices such as distributed control systems (DCS) and programmable logic controllers (PLCs). ) It is composed of smart meters. It monitors the operation of the entire power plant in real time and on-line management, including control, signal, measurement, protection, automatic devices and transmissions, etc. It utilizes computer technology and modern communication technology, through functional combination and optimized design. The implementation of automatic monitoring, measurement control and coordination of power plants is an integrated application of automation and computer and communication technologies in the power sector, which is of great significance for the safe and stable operation of power plants. However, it has the important defect of lack of communication and information sharing with the entire production decision.
The emergence of power plant management information system (MIS) is precisely to solve the problem of integration of production and decision-making information. It is used as the upper-level mechanism of SIS and DCS, and is based on DCS. It uses advanced technology for the purpose of economic operation and improvement of the overall efficiency of power generation enterprises. , Applicable, and effective professional calculation methods to realize information sharing and plant-level production process real-time information monitoring and scheduling throughout the power plant. It provides real-time, effective and reliable real-time operational data for decision-making of power plant management, and provides scientific and accurate economic indicators for companies operating under market conditions.
This article describes the experience of integrating power plant information integrated automation systems (hereafter abbreviated as IT systems) that integrates MIS with SIS and DCS technologies to achieve plant-wide information integration and sharing.
First, the basic structure and system of IT system
In the late 1980s, with the rapid development of computer technology and network technology, the combination of multiple technologies in the process industry enabled process control to break through the islanding model of automation, resulting in the integration of control, optimization, scheduling, management, and operations. The new integrated automation model, ERP/MES/PCS three-layer structure came into being [2]. In the three-tier structure, people hope to realize the comprehensive automation of the enterprise from the three aspects of business management, production management and process control, namely, to establish an enterprise resource planning (ERP) system and a manufacturing execution system (MES-manufacture). Execution system) and process control system (PCS). After the enterprise management decision-making level uses ERP to determine the enterprise product strategy and formulate an optimized production plan, the MES prepares production scheduling instructions from the production scheduling system (PSS) according to the company's equipment, raw materials, etc., and performs production scheduling (or units) for each production device. Optimize the calculation and give an optimized formula or production plan (setpoint) so that the DCS in the control domain can perform real-time operation and control of the underlying industrial production process according to the optimized formulation or production plan.
The key to the IT system is integration [3]. In the integrated system with MES as the core, a more meticulous 5-layer division is made, which is divided into 5 layers: decision-making layer, management layer, execution layer, process control layer, and support layer. , And 2 database systems (relational database systems and real-time database systems). The overall framework is shown in Figure 1.
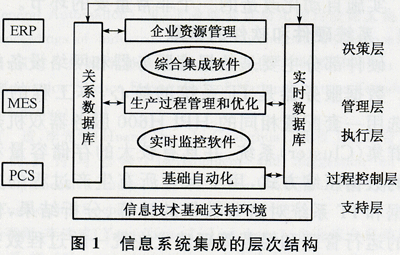
Among them: The decision-making layer includes the enterprise information portal, operation support decision-making, key business indicators and basic information; the management level includes production scheduling, workshop management, supply procurement, sales management, technology management, quality management, financial costs, measurement information, human resources , equipment management, energy management, safety and environmental protection; executive level includes real-time data monitoring, production scheduling, process simulation group, and optimization control; process control layer includes PLC control, DCS control, online quality inspection, data collection, security alarm, etc.; support layer Including information technology basic environment (network, computer equipment, system software, tool software). Wherein, the management layer extracts useful information from the relational database to help the decision, while the execution layer and the process control layer extract various information in the real-time production process from the real-time database to manage and monitor the normal operation of the production, of course, between the two. Data and information can also be exchanged and work together. It can be seen from the above hierarchical structure diagram that the functional modules of each level cooperate with each other and are closely linked together through interfaces to complete the information integration function.
Second, the implementation of IT systems
At present, many power plants have already equipped MIS and DCS equipment. The design of the IT system is based on computer and network technology, giving full play to the experience and creativity of all levels of management personnel, and optimizing the enterprise information resources by means of human-machine discussion [4], from operation, maintenance and operation On the one hand, it conducts decision-making consultation on the behavior of the electricity market in order to achieve integrated automation of information in power plants. The IT system made up for the shortcomings of MIS and DCS from aspects such as economic analysis and overall adjustment. It has become a bridge between MIS and DCS in terms of structure, and has made better use of the company's information to provide a favorable basis for production decisions.
The overall goal of the integrated management and control system for a 600MW unit in a Dingzhou Power Plant is to achieve economical operation of the unit on the basis of high-level unit-level unit control, and to gradually realize economic optimization scheduling and plant-wide economic optimization of the unit group. Management [5]. The system structure is shown in Figure 2.
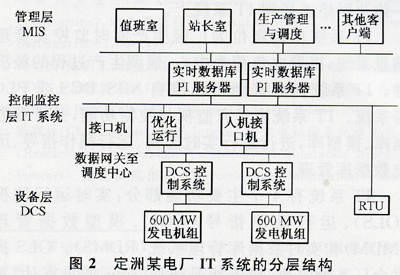
IT system uses client/server (C/S) architecture to complete various online monitoring functions of IT system control stations (such as unit performance calculation optimization analysis station, network system management and maintenance station, etc.), and can be seamlessly connected at the lower level of control Network and IT systems are redundant on industrial networks. The IT system real-time information data server provides centralized collection of information and system maintenance. The IT system provides a reliable firewall that protects the security of user information. Its rich and flexible client software package enables users to handle all of the maximum amount of production information in their hands. These client applications run under the familiar Windows and browser environment.
According to the principle of unified layout of the whole plant network, the design of network topology and equipment identification shall be carried out. The basic design principles are as follows: 1 1000Mbit/s fiber-optic Ethernet is used between each building group of the plant and the information backbone system; 100Mbit/s fiber-optic Ethernet is used between the control systems of the 2 floors and each unit; 3 the control of the main building The room is connected by l0Mbit.s-1/100Mbit.s-1 fiber optic Ethernet; 4 the office building and the main plant room are connected by Category 5 twisted-pair; 5 the backbone network adopts imported brand-name switches; 6 the work is taken between the outlets of the systems Group switch.
The advantages of adopting the integrated layout of the whole plant network system are: stable and reliable system; effective guarantee of network performance; easy maintenance and overhaul; easy upgrade and expansion;
The IT system uses a multi-layer C/S structure to minimize the communication conversion between systems. Balance data traffic between servers and different clients. The configuration principles are: 1 IT system interface station and DCS, PLC is connected in the form of a unified OPC server; 2 real-time data processing using high-performance redundant real-time data server; 3 application server to complete real-time tasks using industrial Ethernet and standard API interfaces and The control system is directly connected. Xinhua uses the load distribution station to directly connect to the control network of the DCS and also serves as a redundant site of the control system. 4 The relational database server interface through DBC and MIS; 5 The management application adopts the Web server method. Connection (optional); 6 All administrative clients are connected to the IT system through a factory-wide integrated network.
The IT system functions as a factory-level production real-time monitoring and management information system, focusing on the power generation load and emphasizing the economics of the production process. IT system information sources can be taken from systems such as MIS, DCS, or PLC. The IT system should have monitoring and control functions, with a database, a model library, and run real-time monitoring, operation and operation guidance, and historical database management.
The IT system has four main functional parts: OLS, OGI, Model Data Management (MDM) and Real-time Database Management System (RDMS). OLS provides plant-wide system monitoring, equipment condition assessment, and plant-wide energy auditing. It corresponds to DAS of DCS and realizes: 1Real-time information display of each thermal system of the whole plant; 2Generation of various required reports; 3Diagnostics of thermal system equipment failure , anticipation and defect management. OGI is based on the evaluation of operational economy, and proposes adjustment opinions due to operational parameter deviations, including load optimization allocation and operation optimization guidance, which is equivalent to MCS of DCS. MDM has data management functions for historical databases and calculation models, provides historical data query, supports modification of calculation model parameters, and is similar to the HSR function of DCS. The main function of RDMS is to store and manage real-time information at the production site, provide basis for enterprise decision-making and production scheduling, and also enable online inquiry to provide useful and real-time information and data for the first three functions.
Third, the key technologies
3.1 The use of real-time database
Since China's industrial companies currently implement the production process control and enterprise management information system in blocks, the system is completed after the two independent islands, there is a "slit" between the two, and the real-time database is An effective platform tool for filling "slits" between the two. The real-time database is the core of the plant-level monitoring information system[6]. Unlike Sybase and Oracle, the real-time database stores production data on a long-term basis in the prototype of the data, which can meet the requirements for fast and efficient data acquisition, storage, and display. The time accuracy of the saved data can reach microseconds. The real-time database is a standard C/S structure and has good openness and scalability. The scale is from 1000 points to several hundred thousand points. The structure is flexible and scalable. It supports multi-platform structure and multi-server structure. The significant difference between real-time databases and relational databases is that advanced data compression technology enables hundreds of thousands of points of production data to be stored on-line for a long period of time (at least for 3 years) with the data's original time and accuracy, which greatly reduces the Data storage space; Powerful data source interface functions (PI database has more than 300 interface functions), these interface functions ensure that the real-time database and most of the control system connection, to meet its wide range of application requirements. The realization of real-time database is an indispensable part of power plant IT system. It provides effective and timely data and information for management, decision-making, production, optimization and other institutions. It is a very important part of the automation transformation of power plants.
3.2 System Hardware and Software Selection
The hardware part is mainly the selection of database server and network equipment. The data server is the core of the IT system. The server of this project uses a dual-system hot-swap cluster system with the same HPL600 server configuration, and has a large storage capacity and advanced data compression methods to save all production processes. The real-time data and IT system's calculation and analysis results of these data make the whole plant's operation management and operation management based on the unified process data. In terms of network devices, the choice of core switches is mainly [7]. The core of the IT system is the redundantly configured 3Com high-performance Switch 4007 switch with high stability and scalability. Its 1000Mbit/s communication port can communicate with data collection switches and MISs for high-speed, large-volume data transmission. At the same time, the high-speed backplane bandwidth of the Switch 4007 supports multiple full-duplex 48 Gbit/s ports, enabling DCS, centralized water-ash control systems, remote terminal units (RTU), MIS, and other interface systems and servers for each unit. High-speed parallel communications. Through the 3Com 1000Mbit/s workgroup switch, each functional station in the IT system can quickly access the information of the real-time database.
The software mainly includes the software in the real-time database and the software in the MIS. The stable and reliable OSI real-time database PI of the US OSI is used as the core database of the real-time monitoring information system of a power plant in Dingzhou. OSI has made great efforts at the PI system client to make it fully compatible with the Windows 95/98 architecture, and its client products have been certified by Microsoft. In addition, the powerful standard application interface is also a major advantage of PI. In the MIS layer, according to the requirements of production management, maintenance management and equipment management, we use IFS/APPLICATION (enterprise asset management and maintenance and maintenance management system) and SAP software as the application software to realize the whole plant production management.
IV. Conclusion
After the implementation of the IT system, the operation was stable and the performance was good. It achieved the intended purpose and was recognized by the users. However, due to the high purchase price of PI series software, and many of these functions are not needed, we have developed and researched real-time database software. The currently-developed XSIS system has been able to replace PI to complete daily production and is already in Xingtai. The power plant is put into operation. It is not as powerful as the PI on the application interface. In terms of hardware, PC and PC servers can be used instead of dedicated database servers, which reduces the development of interface programs and reduces equipment costs.
Fixed Head Lathe / Turning Machine
Fixed Head Lathe,Fixed Head Cnc Lathe,Turning Machine,Turning Lathe
Ningbo Leyan Machinery Technology Co., Ltd , https://www.cncleyan.com