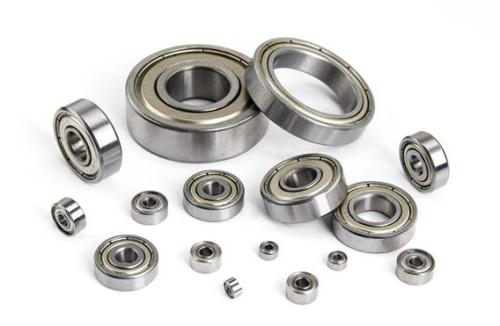
Bearing grinding machines are indispensable components for the equipment manufacturing industry. They are widely used in the fields of construction machinery, agricultural machinery, transportation, defense, aerospace, household appliances, office machinery and high-tech (atoms, nuclear reactors, etc.) and their quality. The pros and cons of life and reliability directly determine the performance of the host. Although China's bearing output was affected by the financial crisis, the growth rate slowed down in 2008 and 2009, but the overall growth rate in the past five years, the average annual compound growth rate reached 20.56%, in 2010 the production capacity has exceeded 20 billion sets, year-on-year growth With a rate of more than 60%, the output reaches 15 billion sets, which accounts for about 10% of the total global market. There are more than 70,000 specifications for bearings, ranging from 0.207mm in inner diameter to 6.2m in outer diameter. The precision is from the ordinary grade to the precision grade, and the bearings produced meet the requirements. More than 70% of the products needed by the country and more than 90% of the required quantities.
At present, China's bearing industry has a large industrial scale surface grinder, in 2010 the industry's main business income reached 126 billion yuan, ranking third in the world. In 2011, influenced by the slowdown of the macroeconomic growth, the main business income of the bearing industry reached RMB 142 billion, and the total output was 18 billion units, with the growth rates of 12.70% and 20.00%, respectively, which fell compared to the growth rate in 2010. According to the estimation of China Bearing Industry Association, in 2012, the main business income of the bearing industry will reach around 158 billion yuan, the growth rate is about 11%; bearing production will reach about 21 billion sets, with the growth rate of about 16%.
In 2011, the overall operating income of the bearing industry continued to grow, but the operating income of the Tianma shares' bearing segment decreased year-on-year. This was mainly due to the fact that Tianma’s shares were affected by factors such as the significant drop in new installed capacity in the wind power industry, making wind power one of the company’s leading products. Bearing sales revenue decreased by 49.93% year-on-year to RMB 368 million, resulting in a year-on-year decrease in operating income from the bearing segment of the company by 28.67% to RMB 1.779 billion.
After decades of efforts, China's bearing industry has formed three major bearing manufacturing bases in Harbin, Wafangdian and Luoyang, private bearing companies in Zhejiang and Jiangsu, and international bearing manufacturing companies (such as Sweden's SKF, Germany's Schaeffler, and the United States. Timken, and Japan's NSK, NTN, etc.) Joint venture or wholly-owned company based industrial structure. As of 2011, there were 1,850 companies in the industry with sales revenues of more than 5 million yuan, and state-owned enterprises, private enterprises, and foreign-funded enterprises accounted for 14%, 66%, and 20% respectively of sales. Luo Baihui, an industry expert, said that in terms of product structure, although China’s bearing industry has developed rapidly in recent years, it is mainly concentrated in the field of ordinary bearings. The demand for high-quality bearings depends on imports. Most of the bearings produced in China are small and medium-sized and small-sized bearings, and the proportion of bearings in medium and large sizes is less than 3%. In the current domestic market, the demand for high-value-added precision and large-size bearings has reached a compound growth rate of about 20%. In particular, market demand for precision bearings for grinding machines, construction machinery, large-scale bearings for heavy-duty rolling mills, and bearings for high-tech applications is strong. It is estimated that in 2014, the main business income of the domestic bearing industry will reach 200 billion yuan.
Nickel-based alloy powders are commonly used in plasma transfer arc welding (PTAW) due to their excellent corrosion resistance, high temperature strength, and good weldability. These alloys are typically composed of nickel as the base metal, with various alloying elements added to enhance specific properties.
Some commonly used nickel-based alloy powders for PTAW include:
1. Inconel 625: This alloy powder is widely used for PTAW due to its high strength, excellent resistance to corrosion, and oxidation at elevated temperatures. It is commonly used in applications involving seawater, chemical processing, and aerospace industries.
2. Hastelloy X: This alloy powder is known for its high-temperature strength and oxidation resistance. It is commonly used in applications involving gas turbine engines, industrial furnace components, and chemical processing.
3. Monel 400: This alloy powder is known for its excellent resistance to corrosion, particularly in marine environments. It is commonly used in applications involving seawater, chemical processing, and oil refining.
4. Inconel 718: This alloy powder is known for its high strength, excellent resistance to corrosion, and good weldability. It is commonly used in applications involving aerospace, oil and gas, and nuclear industries.
5. Inconel 601: This alloy powder is known for its excellent resistance to high-temperature oxidation and corrosion. It is commonly used in applications involving heat treatment equipment, chemical processing, and power generation.
These nickel-based alloy powders can be used in PTAW processes to create high-quality welds with excellent mechanical properties and resistance to corrosion and high temperatures.
Inconel Powder,Nickel Powder,Pta Welding Ni Alloy Powder,Laser Cladding Ni Base Powder
Luoyang Golden Egret Geotools Co., Ltd , https://www.lyshieldcutters.com