Â
High-Performance Heavy Lifting Salvage Airbags for Hauling out
1.Usage of Marine Airbags
Ship Launching Marine Airbags, also known as roller bags or ship launching rubber balloon, are made of heavy-duty synthetic-tire-cord layers with inner and out rubber layers in long cylindrical balloon shape. Marine Airbags for Ship Launching and Dry Docking for barge can be used for n Brazil, Indonesia Shipyard especially for barges launching, pull to shore, vessels' haul out and ship landing work.
2.Comparison with other Launch Way
Rollers Bag is a innovative ship launching technology, comparing with "end-on launching", "side ship launching", "float-out". This ship launching technology overcomes the restrictions of fixed launching track of side-launch. Ship launching airbags are accepted by more and more shipyards world wide due to its advantages of saving time, saving investment, flexible, safety. The biggest vessel launched by ship launching airbags up to 100,000 DWT.
3.Material and constructure of Marine Airbag
Inflatable Marine Airbags are to be constructed of an out rubber layer, multilayer heavy-duty synthetic-tire-cord layers, and an inner rubber layer vulcanized firmly. Ship launching marine airbags are cylindrical balloon body, with two conical head and end mouth. Air tightness swivel and air inlet kits are screwed with end mouth. Refer below picture.
1. Synthetic-tire-cord layer -Â Reinforcement layer of the ship launching marine airbags which are made of rubber coated synthetic-tire-cord fabrics. Many synthetic-tire cord layers are twined at ideal angles by unique and patented "Holistic Wrapping Technology". To hold the internal pressure and to distribute the stress evenly. Buoder use the 1870 dtex/2 type synthetic-tire-cord fabric. The warp is over 95 cords per 100 mm in width, and the breaking strength is more than 310N per cord.
2. The outer rubber layer covers the outside of ship launching marine airbags. To protects the cord layers from abrasion and other external forces. This compound has sufficient tensile and tear strength to withstand any weather condition and hard usage.
Â
4.Classification of Roller Marine Air Bags
Ship launching marine airbags are categorized by "ordinary airbags", "high-bearing capacity airbags", and "Super-high-bearing capacity airbags" according to the bearing capacity.
- QP Ordinary airbags -Â the air bag with 3, 4Â or 5Â layers of cord fabricÂ
- QG High-bearing capacity airbags -Â the air bag with 6, 7Â or 8Â layers of cord fabric
- QS Super-high-bearing capacity airbags -Â the air bag with 9, 10 or more layers of cord
The standard diameter of ship launching marine airbags (D) varies such as 0.8m, 1.0m, 1.2m, 1.5m, 1.8m and 2.0m, 2.5 meters etc. The standard effective length of air bag (EL or L) is from 6m to 26m, which should be specified by the user. Other specification ship launching airbags also can be supplied upon request.
5.Performance Parameters of Offhshore marine ships pneumatic rubber airbag
Model | Diameter (m) |
Initial pressure (KPa) |
Rated working pressure, Pe (KPa) |
Bearing capacity (kN/m) | Minimum burst pressure (KPa) |
QP3 | 0.8 | 25 | 130 | 114 | 390 |
1.0 | 18 | 100 | 110 | 300 | |
1.2 | 15 | 85 | 112 | 260 | |
1.5 | 13 | 70 | 115 | 210 | |
QP4 | 0.8 | 35 | 170 | 149 | 510 |
1.0 | 25 | 130 | 143 | 390 | |
1.2 | 20 | 110 | 145 | 330 | |
1.5 | 16 | 90 | 148 | 270 | |
1.8 | 14 | 80 | 158 | 240 | |
QP5 | 0.8 | 48 | 210 | 184 | 630 |
1.0 | 35 | 170 | 186 | 510 | |
1.2 | 28 | 140 | 185 | 420 | |
1.5 | 20 | 110 | 181 | 330 | |
1.8 | 16 | 90 | 178 | 270 | |
QP6 | 1.0 | 45 | 200 | 219 | 600 |
1.2 | 32 | 165 | 217 | 490 | |
1.5 | 25 | 130 | 215 | 390 | |
1.8 | 20 | 110 | 218 | 330 | |
Note: 1. Rated working pressure:±5%. 2. Compress deformation: ±2%. 3. Internal pressure is the reference value. |
Prior to delivery of the ship launching marine airbags, we test every air bag .All Evergreen Maritime ship launching marine airbags are manufactured and tested comply with  ISO 14409 "Ships and marine technology - ship launching air bags certificated by CCS, LR, DNV.Â
6.examples of  marine ships pneumatic rubber airbag
7.Large factory work shop and good environment
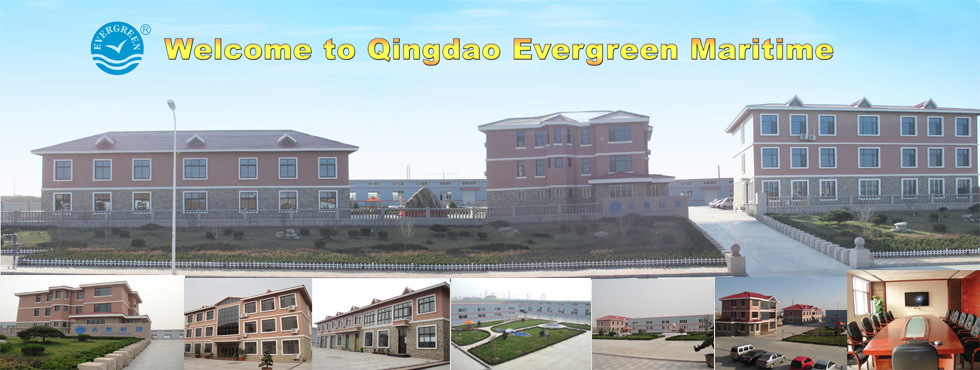
For more information,please contact me directly.
Low-pressure casting was the earliest anti-gravity casting technology, which was first used in industrial production in the 1940s. Nowadays, low-pressure casting is mainly used in the production of aluminum alloy and magnesium alloy parts, such as the automotive hub of the automobile industry, the cylinder body, cylinder head, piston, missile shell, impeller, air guide wheel and other castings with complex shapes and high quality requirements.
The common material of low-pressure casting is A356\ZL101\ZL101A,this kind of material is usually applied to auto part, storage part,transformation part,etc.
The pressure on the surface of the molten metal is 0.06~0.12Mpa.This processing has good shrinkage, casting tissue is dense, easy to produce the large thin-walled complex parts, the casting head is not needed , metal yield can be up to 95%.
Low pressure casting can adopt sand type, metal type, graphite type, etc. The filling process is not only different from gravity casting such as metal casting and sand casting, but also different from high pressure and high speed filling pressure casting, which has the following advantages:
1) Pure metal liquid filling type, which improves the purity of the casting. Because the slag generally floats on the surface of the metal liquid, and the low pressure casting by the metal liquid in the lower part of the crucible realizes the filling through the lifting pipe, which completely avoids the possibility of the slag into the cast cavity.
2) The metal liquid filling type is smooth, reducing or avoiding the turnover, impact and splashing phenomenon of the metal liquid when filling the type, thus reducing the formation of less oxide slag.
3) The casting molding performance is good, the metal liquid filling under the pressure action, can improve the fluidity of the metal liquid, is conducive to the formation of clear outline, smooth surface casting, for the formation of large thin-wall casting is more favorable.
4) The casting crystallizes and solidifies under pressure, which can be fully condensed, and the casting structure is compact.
5) Improve the yield of metal liquid, generally do not need to burst, and the same metal in the lifting tube can be returned to the crucible, reuse, so that the yield of metal liquid greatly increased, the yield can generally reach 90%.
6) Convenient production and operation, good working conditions, high production efficiency, easy to achieve mechanization and automation.
Low pressure casting also has some disadvantages, equipment and mold investment is large; in the production of aluminum alloy casting, crucible and lift pipe long time with metal liquid contact, easy to erosion and scrap, will also make the metal liquid iron and performance deterioration.
Low-pressure Casting Parts,A356 casting parts,A356 low-pressure casting parts,ZL101 casting parts,ZL101 low-pressure casting parts,A356 casting components
NINGBO ZHENHAI BOLANG METAL PRODUCT FACTORY , https://www.diecastingdie.com