The decentralized control system (DCS) is the hub system for the start-up and operation of modern units. The key to distinguishing it from traditional control systems is to have a complete communication system. In recent years, Ethernet technology has developed rapidly, and the network transmission speed has grown from 10 Mbit/s to 1000 Mbit/s, and its use in the DCS backbone communication network has steadily increased.
First, the characteristics of Ethernet communications
(1) Features Ethernet is a LAN that conforms to the IEEE 802.3 standard. Transmission media can be selected from coaxial cables, twisted pair cables, and optical fibers. Its main communication features are random access, carrier monitoring, collision detection, and conflict competition. During each station sending a frame, it is necessary to monitor the network first. If the network is busy, it will continue monitoring. If it is idle, it will send data. Once a collision is detected, the transmission will be stopped immediately and a series of blocking signals will be sent to the bus to inform each bus. Station collisions have occurred so that the capacity of the channel is not wasted by transmitting corrupted frames.
(2) Advantages and Disadvantages Industrial Ethernet uses the following obvious advantages: easy installation, low cost, good connectivity, and easy portability to high-speed networks. However, when multiple sites listen to idle time and send data at the same time, communication collisions will inevitably occur, and the higher the communication load, the more collisions, and therefore it has the disadvantages of transmission uncertainty and low performance under heavy load. It is considered unsuitable for use in real-time industrial control.
II. Application of Industrial Ethernet in DCS of Zhujiang Power Plant
2.1 DCS network structure of Zhujiang Power Plant
2.1.1 DCS backbone communication network structure
The DCS of Zhujiang Power Plant adopts the XDPS-400 system of Xinhua Control. The network type is Ethernet, the network structure is a bus type, the transmission rate is 0 Mbit/s, the transmission medium is a 50 Ω passive coaxial cable, and the maximum capacity is 254, and the communication capacity is 254 The agreed protocol is a broadcast type, point and point structure (Figure 1).
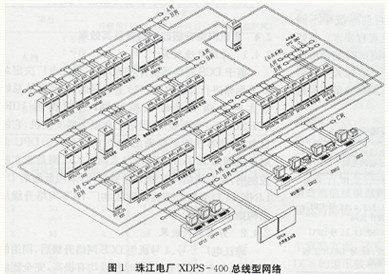
The XDPS-400 is based on a high-speed redundant real-time data network (A network, B network) and an information network (C network) and is composed of multiple nodes. The processing nodes of the linked network are data processing stations (DPUs) and MMI stations (engineering stations, operator stations, historical data stations, intermediate computing stations, and external system interface stations) to form a distribution with process control, sequence control and data monitoring functions. Type control system. The real-time data network is divided into 4 segments. Each segment is connected by a coaxial cable hub and converted to a twisted pair cable to connect to a switching hub (SWITCH HUB) and a bus connection. The information network is used to connect various MMI sites and is used for file transfer and print sharing supported by the operating system.
2.1.2 DPU Distributed Processing Unit Low-level Communication Network Structure
DPU low-level communication uses high-speed serial bus bit bus to connect DPU and I/O unit, communication protocol conforms to EIA RS485 standard, communication transmission rate 375 kbit/s, communication medium is shielded twisted pair STP, adopts command/response communication mode Slave communication structure.
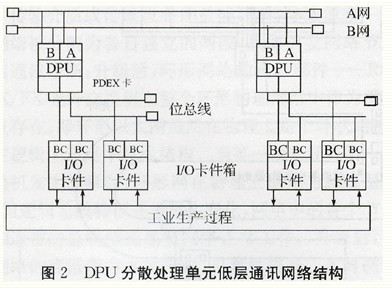
2.2 XDPS-400 System Network Communication Features
The high-speed data communication network is the core of the entire system. Nodes can communicate freely. Nodes can be configured anywhere in the system and are very flexible. Real-time data and real-time status are transparent to each node. Data transmission adopts periodical transmission and exception transmission data exchange to reduce network communication load and ensure reliability. The various nodes on the Internet consist of Intel OEM boards or general-purpose industrial PCs. The network card is also a universal Ethernet card with compatible upgrade capability. Since the information highway uses standard Ethernet and TCP/IP communication protocols, the system is also easy to accommodate other products.
XDPS-400 system network communication technology features:
(1) Provide high-speed data links for broadcasting all online devices. All nodes share the entire XDPS distributed global database without communication bottlenecks.
(2) The dissemination of XDPS real-time data highway information does not require intermediate station storage or forwarding, making the maintenance of the communication network extremely convenient.
(3) All DPU stations and MMI stations are connected to real-time data highways for data communication. All MMI stations are connected to information Ethernet to separate non-real-time management information and real-time control information from each other, thus realizing information control.
2.3 Status Analysis of XDPS-400 System Communication Network Application
2.3.1 Defects in Communication Structure
The XDPS-400 system of Zhujiang Power Plant basically meets the real-time, reliability and safety requirements of the power plant control in application. However, due to the limited technical conditions, the network structure of the system has the following deficiencies.
(1) Higher network load rate Due to the large number of DPUs (36 in total) in Zhujiang Power Plant, although the entire DCS network has been divided into 4 segments, the communication load in each segment is still high, reaching 15% to 20 About %, has exceeded the specification (less than 20%) requirements, resulting in high collision rate, B network reached 11.4%, far greater than the general requirements of the Ethernet collision rate (should not exceed 5%), low efficiency.
(2) I/O bus communication rate is low I/O communication bus communication rate is only 375 kbit/s, the rate is low, and the anti-interference ability is low. In case of accident, it will cause I/O communication error.
(3) If the failure of the backbone network is concentrated as a switch interconnected between network segments, it will result in the failure of one network (A network or B network); if a converter is used to convert the coaxial cable into a twisted pair, Failures will also cause certain segments of the network to fail to communicate with other segments.
2.3.2 Problems in Applications
(1) I/O point jumps occur multiple times, causing automatic adjustment fluctuations. Unit 3 DCS has been paralyzed due to “network storms.†Analysis of the reasons are all related to system network communication, especially the I/O communication bus is The Bitbus approach has a large impact.
(2) Due to the system communication speed problem, the SOE point resolution between different DPUs in the current system cannot meet the requirements of the regulations. The system network load rate is high. When the system unit performance test of Unit 3 was performed, the highest load rate reached 24.5%, and the collision rate reached 11.4%, which was far greater than the requirements of the regulations, which caused transmission delays. The DCS network load rate and collision rate of Zhujiang Power Plant are shown in Table 1.
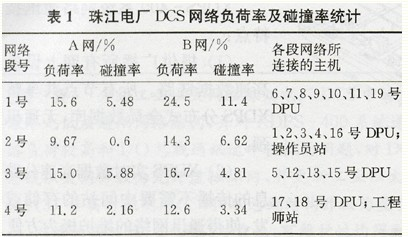
(3) With the development of computer technology, the network card (with BNC interface) of the PCI bus used by the MMI station has been discontinued, and the spare parts are difficult to affect the normal maintenance of the DCS.
(4) If there is a fault in the switch interconnected between the hub and the network segment for conversion, the CRT self-inspection screen has no alarm information and therefore lacks detection and monitoring means.
(5) When the DPU load is high, it will cause information to be changed.
2.4 Communication Network Upgrade and Countermeasures
2.4.1 Upgrade Measures
In view of the problems existing in the DCS network system, Zhujiang Power Plant decided to upgrade the DCS network: (1) The backbone networks A and B were upgraded from the bus Ethernet to the fiber-optic virtual ring network, and were selected by the German HIR-SCHMANN (Hessman). Industrial Ethernet switches, its self-healing, fault-tolerant and other performance can better meet the needs of DCS; (2) DPU low-level communication network upgrade from Bitbus to Ethernet; (3) C network is a non-real-time control network, from the bus structure upgrade to star Structure, using low-cost D-LINK 24-port switch connection. The structure of DCS network upgrade of Zhujiang Power Plant is shown in Figure 3.
2.4.2 Effect After Upgrade
After upgrading the DCS network of No. 2 Unit and No. 4 Unit of Zhujiang Power Plant, the network's real-time performance, safety, reliability and maintainability have been improved, and it can fully meet the power plant control requirements.
(1) Network load rate After the network upgrade, the network load rate is significantly reduced (Table 2), and the communication efficiency is improved.
(2) DPU load rate After the network upgrade, the DPU load rate is reduced by 50% to 80% compared with the original (Table 3), which can avoid the DPU reset phenomenon when the network is abnormal.
(3) The network speed and the speed of the backbone network of communication media are upgraded from 10 Mbit/s to 100 Mbit/s, and the I/O communication rate is upgraded from Bitbus 375 kbitls to BCnet 10 Mbit/s, which improves the real-time performance of network data. Backbone network communication media The use of coaxial cable, which is now replaced by fiber optics, enhances immunity to electromagnetic interference in communications and reduces the chance of I/O drive errors.
(4) Before network security and reliability upgrades, the failure of any transmission medium or transmission equipment in the bus network will cause the original integrated network to be divided into two separate sections, causing disruption of communication between network nodes. After the upgrade, the core component of the ring network, the RS2-FX/FX fabric switch, exists as a logical breakpoint in the entire ring physical network. That is, although the ring Ethernet is physically a ring structure, it is logically a bus. structure. When a certain optical fiber or a certain switch fails, the ring network physically degenerates into a bus network, but the characteristics of the logical bus do not change, and each node in the network works as a normal bus or star network. After the upgrade, the fault-tolerant capability of the entire network is greatly enhanced and reliability is improved. The real-time network is a redundant virtual ring network and has a "self-healing" function. The system can still work after 3 breakpoints (maximum allowable) occur. The I/O bus uses redundant BCnet communication. Compared to the original Bitbus bus, the communication speed is greatly improved, and fault tolerance and fault tolerance are improved.
(5) System maintenance The HIRCHMANN switch has self-test fault output contacts and network detection software, which is conducive to system maintenance.
Third, the conclusion
(1) The application of ring Ethernet technology in DCS of Zhujiang Power Plant is successful. This technology not only retains the features of cheap and efficient Ethernet, good compatibility, but also enhances its real-time performance, reliability and security, and can fully satisfy Power plant production needs; Although Ethernet has the disadvantages of uncertainty and low performance under heavy load, network communication performance can be improved by increasing the rate and reducing the load, so the application of industrial Ethernet in industrial control is feasible.
(2) Ethernet technology has developed rapidly. As the standard is open, DCS manufacturers can easily upgrade the performance of the entire communication system as needed, thus reducing production costs.
(3) A mature DCS, communication network type selection is only an important aspect, there are many other key technologies can improve the overall DCS communication efficiency and communication real-time, such as information compression technology, event reporting technology. Therefore, according to the characteristics and requirements of industrial control, DCS manufacturers should not only properly develop and use communication technologies to improve communication efficiency, but also fully consider various protections during communication failure to ensure industrial control. Safety and reliability.
First, the characteristics of Ethernet communications
(1) Features Ethernet is a LAN that conforms to the IEEE 802.3 standard. Transmission media can be selected from coaxial cables, twisted pair cables, and optical fibers. Its main communication features are random access, carrier monitoring, collision detection, and conflict competition. During each station sending a frame, it is necessary to monitor the network first. If the network is busy, it will continue monitoring. If it is idle, it will send data. Once a collision is detected, the transmission will be stopped immediately and a series of blocking signals will be sent to the bus to inform each bus. Station collisions have occurred so that the capacity of the channel is not wasted by transmitting corrupted frames.
(2) Advantages and Disadvantages Industrial Ethernet uses the following obvious advantages: easy installation, low cost, good connectivity, and easy portability to high-speed networks. However, when multiple sites listen to idle time and send data at the same time, communication collisions will inevitably occur, and the higher the communication load, the more collisions, and therefore it has the disadvantages of transmission uncertainty and low performance under heavy load. It is considered unsuitable for use in real-time industrial control.
II. Application of Industrial Ethernet in DCS of Zhujiang Power Plant
2.1 DCS network structure of Zhujiang Power Plant
2.1.1 DCS backbone communication network structure
The DCS of Zhujiang Power Plant adopts the XDPS-400 system of Xinhua Control. The network type is Ethernet, the network structure is a bus type, the transmission rate is 0 Mbit/s, the transmission medium is a 50 Ω passive coaxial cable, and the maximum capacity is 254, and the communication capacity is 254 The agreed protocol is a broadcast type, point and point structure (Figure 1).
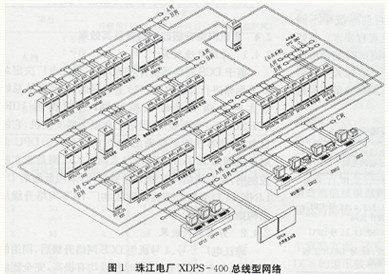
The XDPS-400 is based on a high-speed redundant real-time data network (A network, B network) and an information network (C network) and is composed of multiple nodes. The processing nodes of the linked network are data processing stations (DPUs) and MMI stations (engineering stations, operator stations, historical data stations, intermediate computing stations, and external system interface stations) to form a distribution with process control, sequence control and data monitoring functions. Type control system. The real-time data network is divided into 4 segments. Each segment is connected by a coaxial cable hub and converted to a twisted pair cable to connect to a switching hub (SWITCH HUB) and a bus connection. The information network is used to connect various MMI sites and is used for file transfer and print sharing supported by the operating system.
2.1.2 DPU Distributed Processing Unit Low-level Communication Network Structure
DPU low-level communication uses high-speed serial bus bit bus to connect DPU and I/O unit, communication protocol conforms to EIA RS485 standard, communication transmission rate 375 kbit/s, communication medium is shielded twisted pair STP, adopts command/response communication mode Slave communication structure.
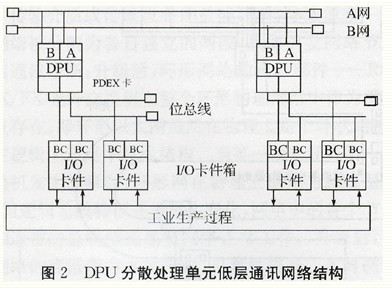
2.2 XDPS-400 System Network Communication Features
The high-speed data communication network is the core of the entire system. Nodes can communicate freely. Nodes can be configured anywhere in the system and are very flexible. Real-time data and real-time status are transparent to each node. Data transmission adopts periodical transmission and exception transmission data exchange to reduce network communication load and ensure reliability. The various nodes on the Internet consist of Intel OEM boards or general-purpose industrial PCs. The network card is also a universal Ethernet card with compatible upgrade capability. Since the information highway uses standard Ethernet and TCP/IP communication protocols, the system is also easy to accommodate other products.
XDPS-400 system network communication technology features:
(1) Provide high-speed data links for broadcasting all online devices. All nodes share the entire XDPS distributed global database without communication bottlenecks.
(2) The dissemination of XDPS real-time data highway information does not require intermediate station storage or forwarding, making the maintenance of the communication network extremely convenient.
(3) All DPU stations and MMI stations are connected to real-time data highways for data communication. All MMI stations are connected to information Ethernet to separate non-real-time management information and real-time control information from each other, thus realizing information control.
2.3 Status Analysis of XDPS-400 System Communication Network Application
2.3.1 Defects in Communication Structure
The XDPS-400 system of Zhujiang Power Plant basically meets the real-time, reliability and safety requirements of the power plant control in application. However, due to the limited technical conditions, the network structure of the system has the following deficiencies.
(1) Higher network load rate Due to the large number of DPUs (36 in total) in Zhujiang Power Plant, although the entire DCS network has been divided into 4 segments, the communication load in each segment is still high, reaching 15% to 20 About %, has exceeded the specification (less than 20%) requirements, resulting in high collision rate, B network reached 11.4%, far greater than the general requirements of the Ethernet collision rate (should not exceed 5%), low efficiency.
(2) I/O bus communication rate is low I/O communication bus communication rate is only 375 kbit/s, the rate is low, and the anti-interference ability is low. In case of accident, it will cause I/O communication error.
(3) If the failure of the backbone network is concentrated as a switch interconnected between network segments, it will result in the failure of one network (A network or B network); if a converter is used to convert the coaxial cable into a twisted pair, Failures will also cause certain segments of the network to fail to communicate with other segments.
2.3.2 Problems in Applications
(1) I/O point jumps occur multiple times, causing automatic adjustment fluctuations. Unit 3 DCS has been paralyzed due to “network storms.†Analysis of the reasons are all related to system network communication, especially the I/O communication bus is The Bitbus approach has a large impact.
(2) Due to the system communication speed problem, the SOE point resolution between different DPUs in the current system cannot meet the requirements of the regulations. The system network load rate is high. When the system unit performance test of Unit 3 was performed, the highest load rate reached 24.5%, and the collision rate reached 11.4%, which was far greater than the requirements of the regulations, which caused transmission delays. The DCS network load rate and collision rate of Zhujiang Power Plant are shown in Table 1.
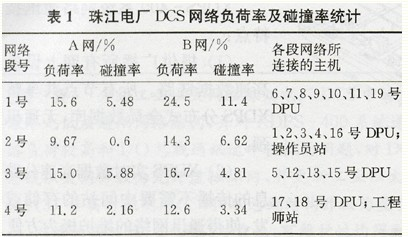
(3) With the development of computer technology, the network card (with BNC interface) of the PCI bus used by the MMI station has been discontinued, and the spare parts are difficult to affect the normal maintenance of the DCS.
(4) If there is a fault in the switch interconnected between the hub and the network segment for conversion, the CRT self-inspection screen has no alarm information and therefore lacks detection and monitoring means.
(5) When the DPU load is high, it will cause information to be changed.
2.4 Communication Network Upgrade and Countermeasures
2.4.1 Upgrade Measures
In view of the problems existing in the DCS network system, Zhujiang Power Plant decided to upgrade the DCS network: (1) The backbone networks A and B were upgraded from the bus Ethernet to the fiber-optic virtual ring network, and were selected by the German HIR-SCHMANN (Hessman). Industrial Ethernet switches, its self-healing, fault-tolerant and other performance can better meet the needs of DCS; (2) DPU low-level communication network upgrade from Bitbus to Ethernet; (3) C network is a non-real-time control network, from the bus structure upgrade to star Structure, using low-cost D-LINK 24-port switch connection. The structure of DCS network upgrade of Zhujiang Power Plant is shown in Figure 3.
2.4.2 Effect After Upgrade
After upgrading the DCS network of No. 2 Unit and No. 4 Unit of Zhujiang Power Plant, the network's real-time performance, safety, reliability and maintainability have been improved, and it can fully meet the power plant control requirements.
(1) Network load rate After the network upgrade, the network load rate is significantly reduced (Table 2), and the communication efficiency is improved.
(2) DPU load rate After the network upgrade, the DPU load rate is reduced by 50% to 80% compared with the original (Table 3), which can avoid the DPU reset phenomenon when the network is abnormal.
(3) The network speed and the speed of the backbone network of communication media are upgraded from 10 Mbit/s to 100 Mbit/s, and the I/O communication rate is upgraded from Bitbus 375 kbitls to BCnet 10 Mbit/s, which improves the real-time performance of network data. Backbone network communication media The use of coaxial cable, which is now replaced by fiber optics, enhances immunity to electromagnetic interference in communications and reduces the chance of I/O drive errors.
(4) Before network security and reliability upgrades, the failure of any transmission medium or transmission equipment in the bus network will cause the original integrated network to be divided into two separate sections, causing disruption of communication between network nodes. After the upgrade, the core component of the ring network, the RS2-FX/FX fabric switch, exists as a logical breakpoint in the entire ring physical network. That is, although the ring Ethernet is physically a ring structure, it is logically a bus. structure. When a certain optical fiber or a certain switch fails, the ring network physically degenerates into a bus network, but the characteristics of the logical bus do not change, and each node in the network works as a normal bus or star network. After the upgrade, the fault-tolerant capability of the entire network is greatly enhanced and reliability is improved. The real-time network is a redundant virtual ring network and has a "self-healing" function. The system can still work after 3 breakpoints (maximum allowable) occur. The I/O bus uses redundant BCnet communication. Compared to the original Bitbus bus, the communication speed is greatly improved, and fault tolerance and fault tolerance are improved.
(5) System maintenance The HIRCHMANN switch has self-test fault output contacts and network detection software, which is conducive to system maintenance.
Third, the conclusion
(1) The application of ring Ethernet technology in DCS of Zhujiang Power Plant is successful. This technology not only retains the features of cheap and efficient Ethernet, good compatibility, but also enhances its real-time performance, reliability and security, and can fully satisfy Power plant production needs; Although Ethernet has the disadvantages of uncertainty and low performance under heavy load, network communication performance can be improved by increasing the rate and reducing the load, so the application of industrial Ethernet in industrial control is feasible.
(2) Ethernet technology has developed rapidly. As the standard is open, DCS manufacturers can easily upgrade the performance of the entire communication system as needed, thus reducing production costs.
(3) A mature DCS, communication network type selection is only an important aspect, there are many other key technologies can improve the overall DCS communication efficiency and communication real-time, such as information compression technology, event reporting technology. Therefore, according to the characteristics and requirements of industrial control, DCS manufacturers should not only properly develop and use communication technologies to improve communication efficiency, but also fully consider various protections during communication failure to ensure industrial control. Safety and reliability.
Badminton Racket Stringing Machine
Badminton Racket Stringing Machines, Badminton Stringing Machines, Badminton Stringing Machines for sale, best Badminton Stringing Machines
Yi He Technology (Shenzhen) Co.,Ltd , https://www.nbball-shootingmachine.com